標準化/現場改善/品質優先の考えが確実な再発防止には大切です。
歯止めを講じるにはフールプルーフ、ポカヨケ対策とフェイルセーフ、ミスに気付く仕組みづくりが必要になります。
再発防止策
標準化
別の記事で、標準化の難しさを記載していますので、そちらを参照ください。簡単に振り返ると
- 標準書が実作業にあっていない。改定がされておらずメンテされていない。
- ○○について確認する。注意して作業する。など、個人の判断でどうとも考えられる表現になっている。
- 過去のトラブルなどを事例を用いて、標準を守らないとどういった不具合があるのか?そこまで教育していない。
- 標準作業が浸透するような工夫が足りない。(例えば、ご褒美制、朝礼での自己宣言など)
それではどうすれば良いかというと、
- 品質管理のポイントを見える化する。(作業:写真+文章、管理項目:チェックシート)
- 標準作業を守らないとどういった不具合が発生するのか十分に納得してもらう。
この2点が大切になると感じています。
現場改善
私が敢えて言うまでもなく基本です。5Sや分かりにくい表示の改正、作業環境の改善、作業方法の改善、などです。ヒューマンエラーの防止や再発防止にとどまらず、作業ミス低減、生産性向上、コストダウンも期待できます。
基本でありながら難しい。
今その状態で出来てしまっているから必要性を感じていない。あるいは、以前提案したけど、お金が無いと断られた。など、理由は色々出てきます。
では、どうすれば良いか?
心理学的に、やる気を引き出すには肯定的な未来を描き、今あるリソースを使って出来ることから実施して行こうといったソリューション・フォーカスという考え方があります。
また、参考図書として「15分ミーティング」のすごい効果、矢本 治 著、日本実業出版社を紹介します。筆者の方が認識されているかどうか分かりませんが、ソリューション・フォーカスの実践版のような本だと思っています。
- 分析は前提、会議では確認の質問のみ
- より良い未来を創るための前向き発言
- 自分たちの出来る事をあらかじめ書く。ひらがな、カタカナ、OK
- 初動は3日内ルールを徹底
良かったら読んでみてください。
品質優先の考え
品質第一とも言われますが、一般には安全第一ですよね。なぜ、安全第一なのでしょう。
これに関しては、昔、勤務していた工場の工場長が言っていた言葉ですが、安全は会社の責任だ。勤務時間の間は従業員を一日家族から預かっている。朝。行ってきますと家をでたら、同じ状態で、ただ今、と帰ってこられるようにする責任が我々にはあるんだ。と言われました。
今でも、覚えていますし、そうなんだろうと思います。
品質は何でしょう。これも責任ですよね。ただ、家族ではなく、お客様に対する責任です。少なくとも私はそう思っています。
良く、納期、コスト、QCDと言われます。ただ、納期もお客様に対する責任ですが、交渉、調整の余地は品質よりもあります。
コストも当然大切です。ただ、どうしてもその品質を確保するのに歩留まりが極端に下がり、コスト的に合わない場合は受けないといった選択をすべきです。過剰品質がコストアップの要因になっていることはありますが、それは全く別の話です。
製造業はどこでも、これらの事を日々葛藤しながら進めているのが現状なのですが、時々、認識違いをされている方がいらっしゃるので、自分の事はさておいて、あえて紹介させていただきました。
作業を受ける側は、問題が起きてから、現実不可能な短納期を受けた営業が悪い。等と言っても何の解決にもなりません。問題を起こしても良いと言った覚えはないと言われて終わりです。
営業側も、製造から危険信号は出されていなかったでしょうか?そこは製造責任で考えるべきだろう。といった態度で接していませんか?
作業指示を出す側(マネージャー)も自問しましょう。調整業務を怠り、無理を現場に押し付けていないでしょうか?
お客様に対して品質の責任を果たすのに、自分は何をすべきなのか考えるのが大切だと思います。
歯止め対策
フールプルーフ、ポカヨケ対策
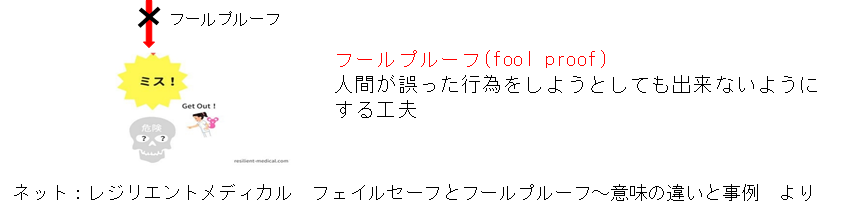
元来は機械設計から出てきた考えのようですが、プロセス設計をする上でも非常にためになる考え方です。ポカヨケの方がなじみがあるかもしれません。人が誤った行為をしようとしても出来ないようにする工夫の事です。
今は、ネットでも事例がたくさん出ているので、参考にすべきと思います。
ポカヨケ改善事例集【図解】 | 日本のものづくり~品質管理、生産管理、設備保全の解説 匠の知恵 (takuminotie.com)や絵で見る創意工夫辞典0304④間違ったら先に進まなくする。にも実例が出ています。
パターン1:センサーで状態を感知し、間違っている時は動作しない
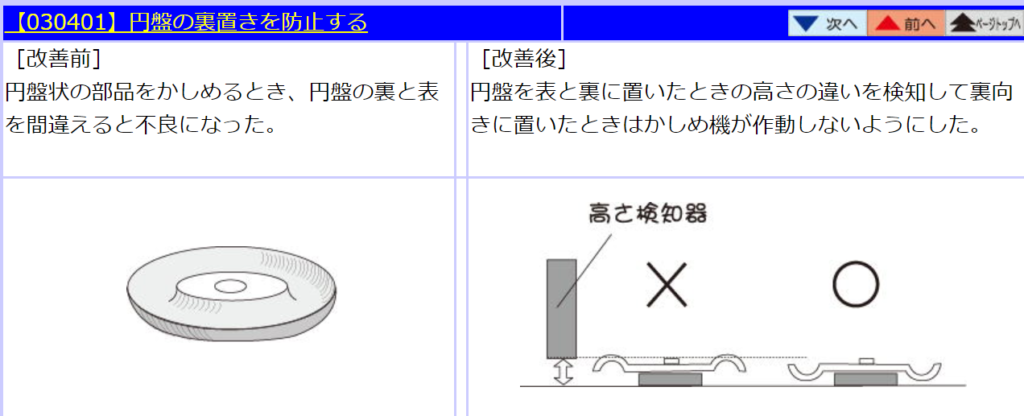
パターン2:セッティングが悪いと形状が合わず、先に進まない。
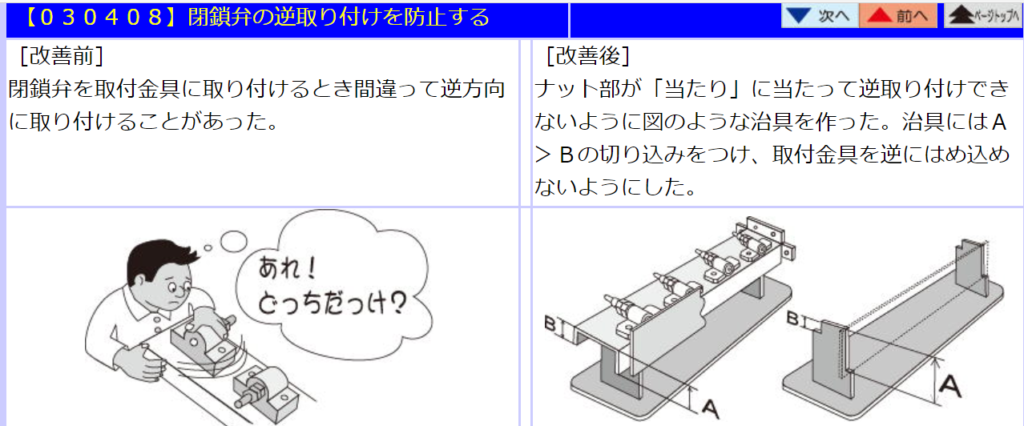
治具は、使いずらいと定着しないことが多いので、注意が必要です。他にも、面白い例が色々でているので、参考にしてください。
フェイルセーフ、ミスに気付く仕組みづくり
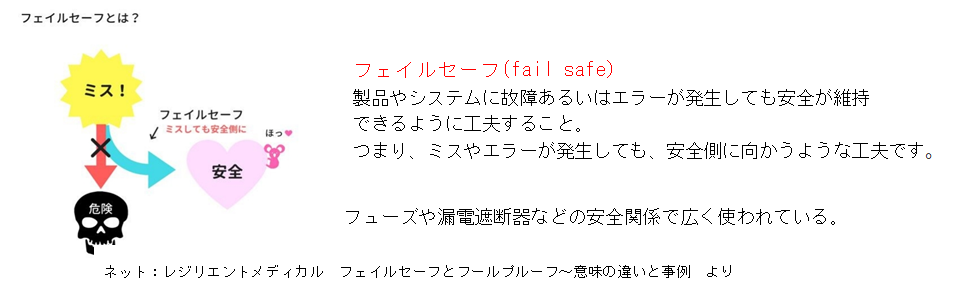
この考えをプロセスに応用しましょう。
ポイントは、ミスが発生した場合に瞬時に作業者が気が付く仕組み作り。です
私がネットで少し調べたところでは、材料加工、組み立て工程であまり良い例が無かったので、私の経験で紹介します。
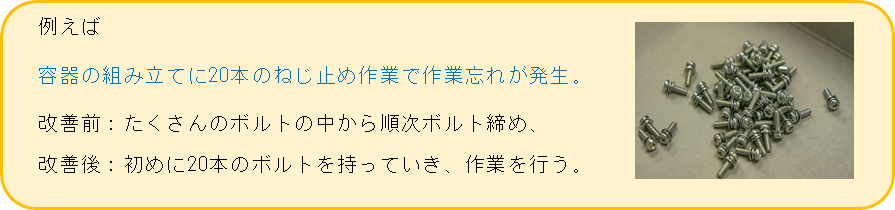
実際にはもっとねじ止めの本数は多いのですが、ネジ止めされていない容器が納入される不具合がありました。良く分かります。作業中に誰かに声をかけられたら、アウトですよね。
加工屋さんには、そのネジで止める箇所は予め分かっているのだから、必要な本数だけ持って行って作業してもらうようにお願いしました。
初めはそんな面倒な事は出来ない。といった対応でしたが、実際にネジ止めしている時に何もしないで見ている人もいます。ネジを数えるのは誰でも出来るので見ている暇が有ったら数を数えてもらいました。
この方法では仮に、最初に数え間違いをしても、数が合わなくなるので良い方法だと思っています。いかがでしょうか?実際のその後はそのような不具合は無くなりました。
まとめ
- 再発防止策の基本は標準化。ただし、以下の点で注意が必要
- 実作業にあっていないなどメンテされていない。
- ○○について確認する。注意して作業する。など、個人の判断でどうとも考えられる表現になっている。
- 標準を守らないとどういった不具合があるのか?教育していない
- 現場改善/品質第一の考えが基本であるがやはり大切
- フールプルーフ、フェイルセーフの思考が大切。
コメント