「品質の教科書」皆川一二 著 日経BPを買って読んでみました。サブタイトルがトヨタ必須の17の品質管理手法を伝授、となっています。
各項目、長年の蓄積があり、世界のトヨタの品質保証体制を支えている考え方で勉強になるところは多いです。しかしながら、未然防止に対しては、色々感じることがあるので紹介させていただきます。
また本の内容をすべて実施するとなると、普通の会社ではかなり難しいだろうというのが正直な印象です。かなりの工夫を考えないといけなくなりそうです。
トヨタの未然防止
未然防止は、問題の発生を予想し、未然に防止することです。まだ起きない問題に対し、発生する前に手を打つことが求められます。まだ起きていない問題であっても、想定外が無いようにしなければなりません。
「品質の教科書」皆川 一二 著、P60~P61より
品質機能展開(QFD)
何故、これが未然防止につながるのか?と思ったのですが、お客様の要望を正確に設計仕様に反映させていないと、要望に沿わない場合には品質不具合になるので、QFDが必要との趣旨のようです。
私も、この辺りはさんざん痛い目を見てきたので大切さは良く分かります。QFDはお客様の要望を網羅的に捉えて、設計仕様に反映する考え方です。
しかし、要望以前の制約条件はQFDでは漏れが発生すると思います。これに関しては、すでに記事にしたように、お客様のラインを良く知って協議する必要があると感じています。良ければ以下の記事を参照ください。
DRBFM[設計FMEA(故障モード影響解析]、工程FMEAについて
DRBMFは(Design Review Based on Failure Mode)の略で設計審査にFMEAを組み込みましょうという事のようです。
FMEA、あるいはFTAに関しては私も記事にしていますのでそちらを参照ください。発生防止の他に流出防止方法についても本では考慮することを進めています。
QAネットワーク
「品質保証の網」を張り、発生防止と流出防止の両面から、問題点を抽出する。これにより、不良品は造らないし、万が一作ったとしても後工程に流さない工夫を施して、社外への不良品の流出を防ぎます。しかし。これだけではありません。費用をかけすぎずに不良品を外に流さないようにすることもQAネットの目的です。
「品質の教科書」皆川 一二 著、P183より
- 発生防止
- どのようにして品質不具合を作らない工程にしているか?
- 流出防止
- どのようにして、流さない工程にしているか?
この2点を掛け合わせて防止レベルを総合的に各工程毎に判断し、全体を見えるようにしたものです。
- 不良が発生しない。:設備的に発生防止、異常検知可能
- 設備や治具で異常を検知する。:4Mが標準化されている。
- 作業標準に頼って作業する。:設備の工程能力はある。勘やコツに頼る要素が少ない。
- 管理が出来ていない。工程能力が不足している。
- 不良が流出しない
- 設備や治具で異常を検知する
- 官能検査で異常を検知する。(目視検査など)
- 要領書が不明確、検出力無し
保証ランクの総合評価
- A:最重要品質保証項目の目標レベル
- B:重要品質保証項目の目標レベル
- C:一般項目の目標レベル
- D~F:不可
上記のように、目標レベルを設定し、横軸に発生防止レベルを縦軸に流出防止レベルをそれぞれ1~4まで取った以下のようなマトリックスとして評価する。
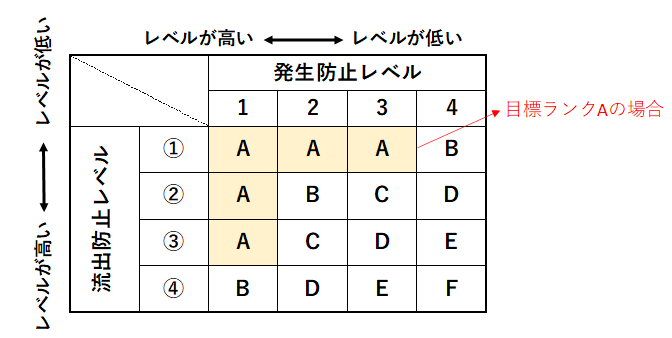
現状の保証ランクと目標とする保証ランクを比べ、低ければ改善、高すぎの場合は見直しを行う。
「品質の教科書」皆川 一二 著、P183~P194から抜粋、引用
一般化、上位概念化とQAネットワークの比較(個人的見解)
QAネットワーク
「品質の教科書」のP284で工程FMEAの実施結果が非の打ちどころがないほど完璧な物であれば論理的に不要と言えるかもしれません。しかし、現実にはすり抜けが発生するので、QAネットワークが必要です。と筆者の方はコメントされています。QAネットワークでは何故漏れが無いと言えるのでしょう?
QAネットワークは、個々の工程の品質保証レベルの見える化を行い、全体のレベルを把握し、全体を最適化するには非常に良い考え方だと思います。
QC工程表を考える場合など非常に有効でしょう。実際にQAネットワークという言葉は知らなくても、QC工程表を考える際は同じような考え方を行います。
未然防止といった観点から言えば、工程FMEAと同じ、特に、FMEAで発生防止と流失防止の2点を盛り込んでいる時点で、結局、同じ事を2回やっているといった印象です。
FMEAに比べて、全体を見渡せ、最適化が出来るといった点ではQAネットワークは有効と思えますが、未然防止といった観点から言えば、FMEAとダブルで実施して、確率を下げているに過ぎないようにQAネットワークを使ったことのない私には見えてしまいます。
一般化と上位概念化
再発防止対策を一般化/上位概念化することで未然防止にまで高めたものと考えています。別の記事で紹介していますので参照してください。
ポイントだけ紹介すると、以下のように、個々の事例を上位概念化し、それを個々の事象に展開することで、未然防止が可能になります。
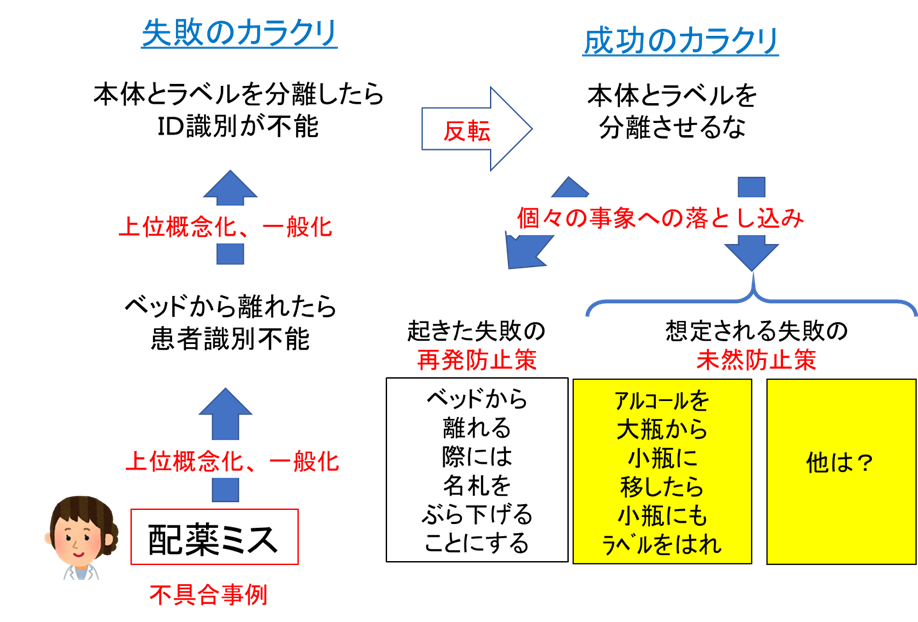
- 過去に発生した不具合事例を上位概念化、一般化し、失敗のカラクリ(一般論)を導く
- 失敗のカラクリを反転させて成功のカラクリを導く。
- 成功のカラクリを個々の事象に落とし込むことで未然防止を図る。
参考図書:失敗学実践編、浜口哲也・平山貴之 著 日科技連出版
QAネットワークもFMEAも想定事項を洗い出すといった点で共通で、想定範囲の広げ方に関しては記載が無いように見えます。一方、過去の事例の一般化/上位概念化を使う事で想定範囲を具体的に広げることが可能になります。
未然防止といった観点で見れば、工程FMEA+一般化/上位概念化の方が有効と感じています。
まとめ
- トヨタの4大未然防止対策:QFD、DRBMF、工程FMEA、QAネットワーク
- QAネットワークは、個々の工程の品質保証レベルの見える化を行い、全体のレベルを把握し、全体を最適化するには非常に良い考え方
- 未然防止の観点で言えば、流失防止も考慮した工程FMEAとQAネットワークは重なるところが多い。
- 別の観点で過去のトラブルの一般化、上位概念化をOAネットワークの代わりに行うことで想定範囲を広げることになるので個人的に推奨。
コメント