なぜリスク対策が必要なのか
- 試作品での評価では絶対的にN数が少ない。実績は圧倒的に少ない。
- 強調試験/寿命評価は無論実施した方が良いが、実体を表していない。
通常、季節変動などを考えると本当に品質的に安定しているのかは1年近くWatchする必要がある。その為、強調試験/寿命評価を実施することが多いが、いずれも疑似評価であって、実体を表しているわけではない。
- 量産前にやるとやらないでは大違い。製造、品保も巻き込んで実施するのがポイント
- 5M+1Eの切り口で考えるのが良い。
設計/開発のメンバーで実施しても効果は薄れる、品保、製造などの他部署のメンバーを参加させるとでより効果的になります。
通常、品質管理の場合4M、(Man/人、Machin/機械、Material/材料、Method/方法)の切り口で間に合うことが多いが、リスク評価の場合にはMeasurement/検査、測定、Environment/環境の5M+1Eで検討する方が効果的です。
FMEAの実施例(他のリスクアセスメントと同じです)
1.FMEAとは?
故障モード影響解析と言われると、非常にとっつきにくいと思われますが、やっていることは一般的なリスクの評価方法、例えば環境リスクメンと、あるいは、安全面でのリスクアセスメントと変わりません。そのような経験のある方には非常になじみやすい方法と言えます。
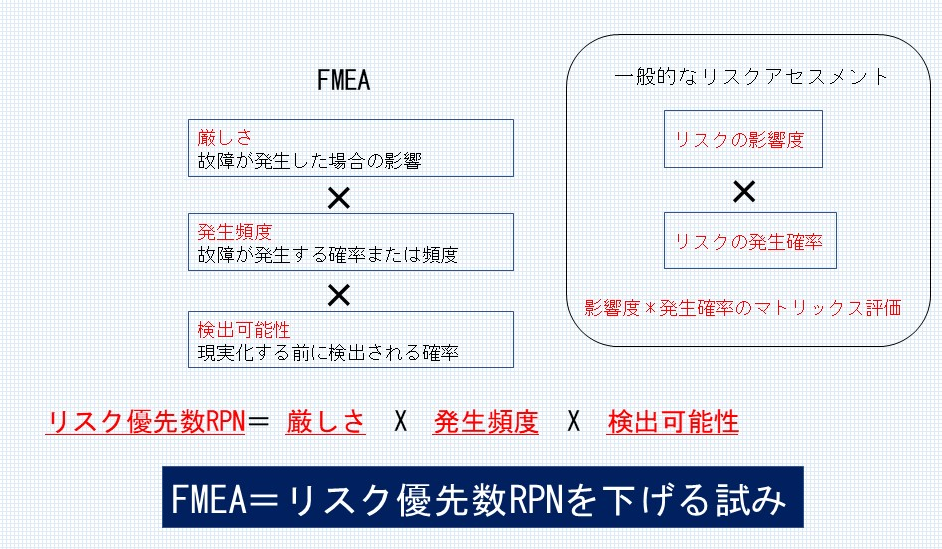
参考文献:FMEAの基礎_故障モード影響解析 日本規格協会 Robin E. Mcdermott, Michael R. Beauregard, Raymond J. Mikulak
FMEAは検出の可能性というのが追加になっていますが、故障が発生しても故障の影響が発生する前に検出される確率を考えているので、発生確率=発生頻度*検出可能性と考えたのがFMEAと見れば通常のリスクアセスメントと同じことを言っています。
2、FMEAの進め方

1、事前準備
各部位の機能をまずは洗い出して機能が発揮できないような故障モード(潜在的故障モード)、その故障が発生した場合の潜在的影響を洗い出す。
2、厳しさを判定する。
- 厳しさ判定基準は公開されているものがあるのでそれを参考にする。(10点満点)
- 故障が発生した場合、負傷や生命の危機が考えられる物(10点)からお客様が故障に気が付かないものまで(1点)
- 点数は司会者が提案する。まとまらない場合はメンバーの投票、平均値を採用すると良い。
3、潜在的故障原因
なぜなぜ分析、議論によって潜在的故障の原因を記入する。
4、発生頻度を判定する。
- 厳しさ判定基準同様公開されているものがあるのでそれを参考にする。(10点満点)
- 1日に一回以上発生するような物(10点)から5年以上で1回発生するような物(1点)まで
5、現行の管理
現行の管理方法を記入する
6、検出の可能性を判定する。
- 厳しさ/発生頻度の判定基準同様公開されているものがあるのでそれを参考にする。
- 検査せていない。あるいは検査できない物(10点)から確実に検査できる物(1点)まで
厳しさ/発生頻度/検出の可能性の判定基準は、例えば、FMEAの基礎_故障モード影響解析 日本規格協会 等を参照してください。
7、リスク優先数を計算する
リスク計算数=厳しさ*発生頻度*検出可能性
8、対策を打つ故障モードを特定する
リスク優先数が何点以上であれば対策を打つ、あるいは、点数の高い、Best3などとして対策を打つのが良い。
9、リスクを下げる処置を決める。
10、リスク評価を再度実施する。
厳しさ/発生頻度/検出可能性を再度評価してリスクが下がったことを確認します。
FMEAの問題点は?
1、時間が非常にかかる。
網羅的に実施できるといったのが利点であるが、その分、検討する項目が多く、非常に時間がかかる。
2、事前準備の精度/洗い出しの精度に影響される
他のアセスメントも同じだが、事前準備の精度がリスクアセスメントの精度に反映される。必ず数人で議論しながら実施する事が大切である。
3、開発初期の段階には不向き、量産前の実施が必要
最後に
FMEAは良い方法ですが、現実的には非常に時間がかかります。具体的には他の方法との組み合わせで、リスク評価を実施しています。具体的には下記の記事を参照ください
コメント