お客様で不具合が発生したら、極力、発生したままの状態で触らずに放置してもらい、現場に駆けつけ現場検証するのが基本です。
現場検証を十分にすることで、原因追及につながる多くのヒントが見えてきます。
お客様に呼び出される場合は営業任せにしてはダメです。貴重な情報が得られるチャンスですから必ず技術も同席しましょう。場合によっては、その時点で原因が分かる事も多々あります。
商品だけ、別の所に移動されていることが良くありますが、出来れば、どのような状態で確認されたのか、現場を確認させてもらいましょう。
社内で発生した不具合なら、迷わず、駆け付け、それが無理ならビデオですぐに確認しましょう。
現物の調査
製造工程との因果関係を調べる
現物を確認する上で、大切なことは、その発生場所、特徴など、何か、汚れがついている。あるいは傷がついているとなると、その発生場所、特徴などから、発生工程を推察することも可能です。
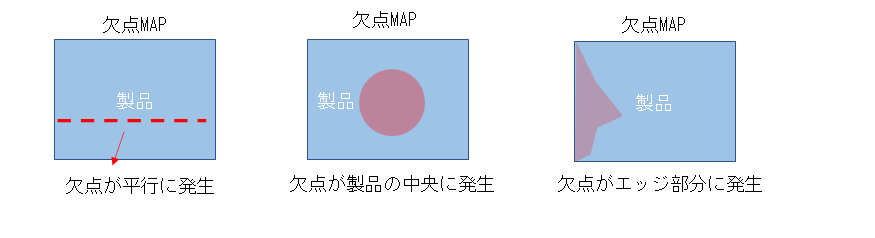
例えば、
欠点が平行に発生する場合、製品がそもそも平行に流れる工程が発生源か?と推定で出来ます。
欠点が中央部に発生する場合(あるいは特定の場所に発生する場合)、中央部に該当する何かが無いか?例えば、上から何かを噴霧するような工程での液だれが無いか?等です。
欠点がエッジ部分に集中している場合、端面に接触するような工程がないか?例えばローラーで左から転がすようなイメージ
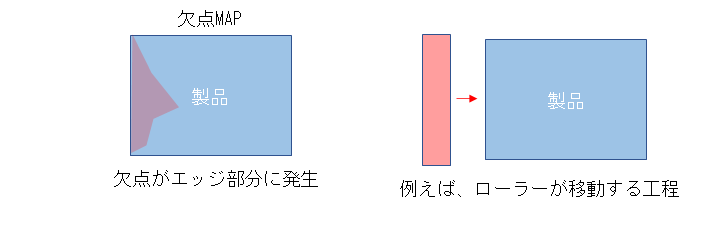
破断の場合、破断面の観察
金属やガラス、セラミックなどの無機材料は破損した場合にはその破断面を観察することで、破壊のモードや破壊の起点、強度劣化の原因など色々分かることが多いので材料が破損した場合には必ず観察します。詳しくは各種専門書を参照ください。
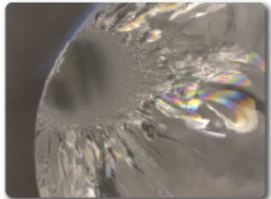
左の写真は都産技研のホームぺージから引用したガラスの破断面の観察結果です。
この監察結果から、割れの発生起点、割れた時の破壊応力が分かります。
汚れの場合、成分分析/同定
欠点の物質が同定できれば、その物質が使われている個所を特定すればよいです。
ただし、微量すぎて、同定までは至らず、何らかの有機物がついているぐらいしかわからない場合が多々あります。
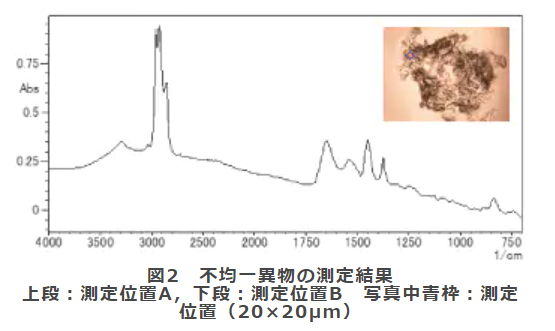
イメージを持っていただくために、SHIMADZUさんのホームページからFTIRの分析結果(チャート)を添付します。
FTIRによる異物分析 -異物スペクトルの扱い方- : 株式会社島津製作所 (shimadzu.co.jp)
有機物を同定する分析方法です。
分析装置を持っていない場合。
民間、あるいは、国の試験所でスポット的に分析してもらうことも可能です。企業規模により料金が異なりますが、概ね、数万円程度のようです。参考までに、都産業研ホームページを添付しておきます。
3.2 機器分析 – 都産技研ホームページ (iri-tokyo.jp)
傷/変形の場合、状態を定量的に観察する
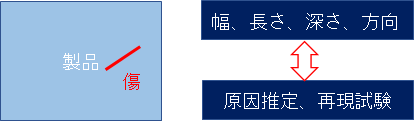
傷/割れ/変形の場合はその程度を定量的に把握し、観察します。傷は方向性など、詳しく調べることで、何が原因なのか推定するのに非常に役立ちます。
内容/現場/現物確認で大切な事 まとめ
- 不具合確認時には、お客様のインパクトを連絡することが大切。
- 現場確認が基本、現場に駆けつけられなければ、ビデオで情報共有する。
- 現物の確認は原因追及につながる必要な調査項目を確実に実施し、発生工程を絞り込む
コメント