QCの7つ道具に入っている管理図は工程の品質状況を見える化した物と言えます。管理図では何が正常で、何が異常なのか、その境界線を明確にする事が大切です。
しかし、よく言われるように検査で品質は作れません。
製品の品質は結果でしかないので、やはり、品質を管理するには原因となる製造プロセスを適切に管理することが非常に大切になります。
品質特性の正常/異常を判定する
正規分布と工程能力Cp、Cpk
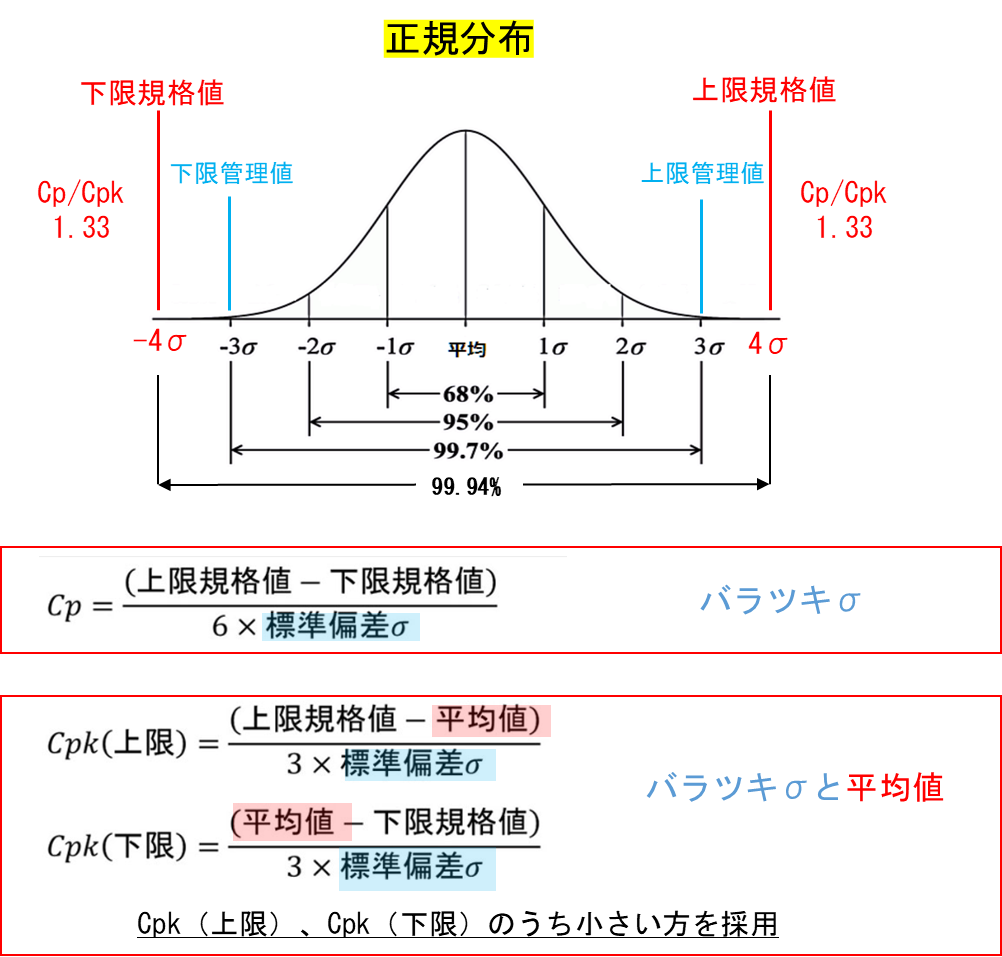
♦正規分布
研磨加工で言えば、板厚や表面粗さといった計測可能な品質特性は、ヒストグラムを作ると平均値が一番多く、平均値から遠ざかるにしたがって少なくなる、いわゆる正規分布に従います。正規分布は、平均値と標準偏差σ(バラツキ)によって決まります。
♦工程能力
製品を作る場合は当然規格値(スペック)がありますので、規格値に対して、どのくらい余裕が有るかを指数化した物が工程能力Cp、Cpkと呼ばれるものです。
Cp、Cpkは上記に示したように、品質特性の規格幅を6σで割った値になります。Cpkは平均値がずれた場合を想定していますが、結局同じものです。Cpkは片側規格にも使え、上限と下限で値の小さい方を採用します。
♦工程能力1.33とは
一般に工程能力は1.33以上あれば十分と言われています。しかし、上記のヒストグラムで考えれば上記のようになり、10000個検査したら7個は不良品が混入するレベルになります。
工程内検査
私は工程内検査の目的は以下の二つであると認識しています。
- 製造した半製品を次工程に送って良いかどうか判断するロットの合否判定(AQL)
- 品質の異常を検出し、製造条件や必要な部署にFeed Backして。具体的なアクションにつなげる事。(管理図)
ロットの合否判定は通常、AQLの考え方を使って合否判定を行います。ある検査基準を決めて、許容する不良混入率を想定し、ロットサイズから必要なサンプル数を決めて、NG(スペックアウト、規格外)が何個までであればそのロットを合格とするものです。
しかし、忠実に実施しようとするとロットサイズが大きくする必要が出て来ます。品質の重要度によって総合的にサンプル数は決定するのが良いと思います。
管理図
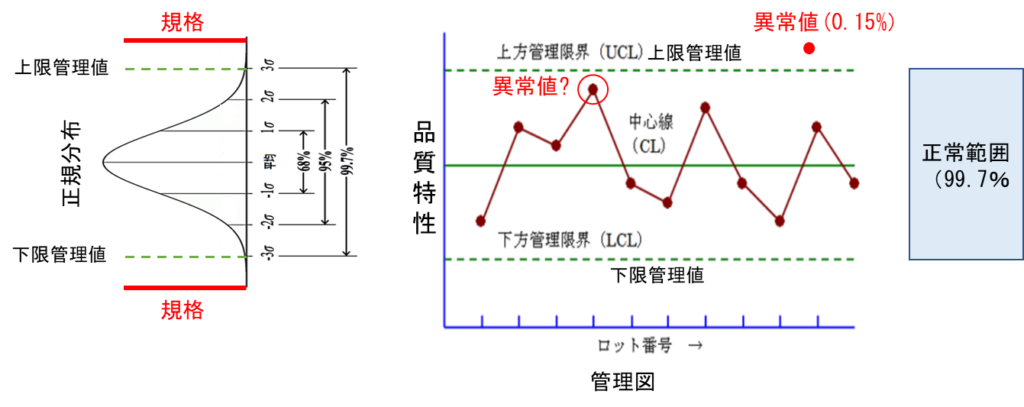
管理図とは上記のように、品質特性の折れ線データと中心線(狙い値)、管理線からなるグラフで、品質に異常がないか判断する図の事です。
折れ線のデータは、N=1であれば測定値そのものを載せますが、通常は平均値やレンジRを用います。Nがロット当たりのサンプル数が20個以上あるのならレンジの代わりに標準偏差σを使っても良いでしょう。
品質特性の異常と正常の判定基準
上記は工程能力が1.33の場合を想定しています。規格が4σの所に有る場合です。
管理値は規格より厳しくしなければならないので、通常3σの所に管理線を引くことになります。
♦管理線を超えた場合
この場合は問題なく異常と判定すべきでしょう
しかし、管理線を越えてもこの場合、そもそも0.3%の確率で発生します。(片側であれば0.15%)良品が多く含まれていること考えられます。従って、該当ロットは一旦、保留品として扱い、全数検査や再加工のような処置を決める事になります。
また、狙い値をターゲットに近づけるように製造条件を管理範囲内で調整することになります。
♦正常範囲内でも管理線に近い場合は?
上記の図のようにギリギリ超えていないような場合は異常でしょうか?
私は勉強不足で知らなかったのですが、シューハート管理図 というのが有って、正常の範囲内でも異常とみなすのに8つのルールが有るとされています。
一つは、管理線を越えた場合なので問題はないですが、正常の場合、特異な傾向がみられる7つのパターンは異常とみなすべきとしています。(詳しくは、シューハート管理図 8つの異常ルール と検索してください。)
私は単純に知らなかったので使ったことは無いですが、あまり実用的ではないような気がします。
私の場合はもっぱら上記の図のように、管理線のギリギリ下。具体的には2.5σから3σの場合、N増し評価を実施してやはり2.5σ~3σに入るような場合、異常品として保留扱いとしていました。
また、平均で見ている場合は生データーを見て、1点でも管理線を越えていれば異常品としていました。
管理図の限界
ヒストグラムによる確認
そもそも、管理図はヒストグラムが正規分布に従う前提で成り立っています。なので、実際にヒストグラムを作ってその形を確認して行く事が品質を改善する(工程能力を上げる)上では大切になります。
しかし、ヒストグラムにして確認するのは毎日実施できるような仕事でもありません。管理図で異常が認められた時には原因追及のためにヒストグラムで全体像を確認するのが大切だと思っています。

ヒストグラムの形から原因を探るにはどうすれば良いのかに関しては上記のサイトが分かりやすかったので良ければ参照ください。
ヒストグラムの限界
ヒストグラムはあくまでも、品質特性という結果を示したものに過ぎません。なぜ、その品質になったのか原因を探るには製造時に異常が無かった見えるようにしておく事が必要になります。
ですので、製造時に異常が無かったかどうか、見える化してわかるようにしておく事が非常に大切になります。
生産工程の見える化
推移グラフ
♦管理特性
ガラスの研磨で言えば、加工圧力や回転数、砥粒濃度など、管理値を必要とする管理特性は設定値です。そもそも正規分布にならないので管理図にしても意味は有りませんが、推移グラフを作り、傾向を見えるようにすることが大切です。
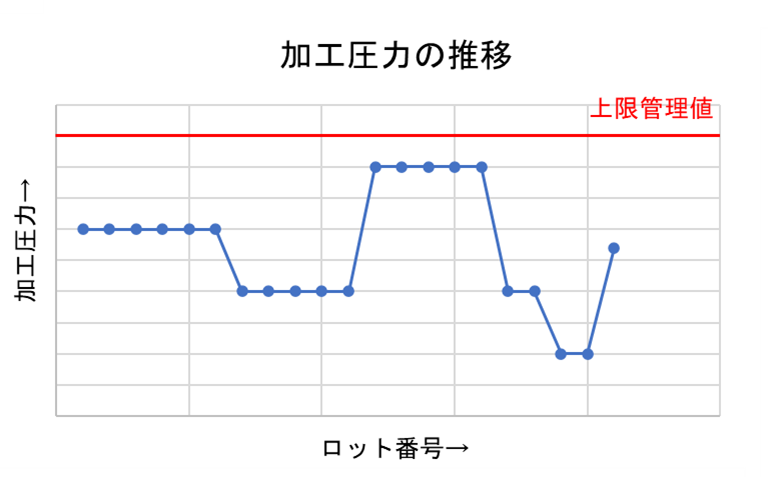
横軸はロット番号ではなく日時でも良いですが、後で管理図との照合が必要になります。
♦モニター
例えば温度や湿度などです。
作業標準
作業標準書で作業は標準化しておく事は基本です。しかし、 普通は標準書を見て作業などしません。
■写真/作業方法での見える化
実作業の際に注意喚起を目的として、写真に管理項目を入れ込んだ資料を作り、現場の見えるところに掲示する方法がお勧めです。
■チェックシートで見える化
チェックシートでポイントを確認してもらうことも大切です。標準書よりは現場で活用されやすく、必要な情報もまとまっているので作業標準書よりはメンテしやすいです。
異音、異臭、色、触感など
数値化、言語化出来ないですが、実は大切な情報です。しかし、普段から意識をしていないと異常かどうかわかりません。逆に言えば、意識をしていると、分かるようになります。
異音、異臭については3段階で評価をしてもらって、異音、異臭を感じた場合は、どのような異音であったか、どのような異臭であったか言葉で記録してもらう事が大切と思います。
生産工程の異常の判断
製造の装置が、明らかにいつもと動きが違うなど、装置上のトラブルが有った場合に保留扱いにしていました。
私の経験から言えば、推移グラフや異音、異臭から異常ロットと判断して保留扱いにしたことは有りません。もっぱら、品質特性で異常が有った時の原因追及のために使用するといった事が殆どでした。
情報の取り扱いは、ケースバイケースで決めれば良いと思いますが、大切なのは、各情報を作業者も含めて、誰でもみて分かるように共有出来ている事だと思います。
そうすることで、一人では気が付かない工程の異常が早く明確になり対応も早くとれるのではないかと思います。
まとめ
- 規格値に対して、どのくらい余裕が有るかを指数化した物が工程能力Cp、Cpkである。
- 工程能力が1.33以上あると工程能力は十分とされ、抜き取り検査は可能と言われている。
- 管理図とは品質特性の折れ線データと中心線(狙い値)、管理線からなるグラフで、品質に異常な傾向が見えないか判断する図の事である。
- 通常は±3σを管理線とし、越えたものは異常品として保留扱いにし、全数検査や再加工を行う。
- 管理線以下でもどういった場合に異常扱いにするのかについては、別途決めておく事が大切になる。
- 工程を改善するには管理図では不十分で、品質特性をヒストグラムとしその形から原因を考える必要が有る。
- 生産工程の見える化を図ることが、工程能力の悪化の原因追及には大切である。
コメント