品質問題を起こす原因として人に起因するトラブルもあり、避けては通れません。これに関して、どのように原因を追究して行けばよいのか紹介したいと思います。
人に起因するトラブルのタイプ
人に起因するトラブルの原因によって分類すると、次のように考えられます。
標準の内容を知らなかった。理解していなかった。また、作業標準通りに行う技能を持っていなかった。
標準も理解し、能力もあるが、非常に急がされていたので、このぐらい大丈夫だろうと思った。等の理由により意図的に守らなかった。
標準も理解し、能力もあり、正しい事をしているつもりだった。にもかかわらず。意に反してトラブルになってしまった。
タイプ別の対策
知識/技能が不足している時の対策
これに対しては、教育、訓練しかないと思われます。
でも、何故、知識/技能の不足しているメンバーに作業させたのでしょう?
- 認定者しか作業させない
- 見習い期間を定め、その間はしばらくは出来上がりを第3者に確認させる
等が対策として思い当たります。人で不足、など色々な状況があるでしょうから、状況に合わせて何が出来るか考えましょう。
自己判断によるミスの対策
個人の判断を優先させたということは、標準作業を軽視しているということです。
勝手に判断するな。というのは簡単ですが、それだけでは不十分ですよね。何故、大丈夫だと思ったのか深堀しましょう。
その際、行為そのものについて確認するようにし、人格や、何故については触れないようにしましょう。
悪質な場合はやはり毅然とした態度で臨まないと示しがつかない場合もありますが、その場合も行為を咎めましょう。
標準書の問題点があらわになるチャンスでもあります。しっかり見直しましょう。
標準書内容は十分か?
以下のような問題で、標準作業が軽視されたのではないでしょうか?
- 標準書が実作業にあっていない。改定がされておらずメンテされていない。
- ○○について確認する。注意して作業する。など、個人の判断でどうとも考えられる表現になっている。
- 過去のトラブルなどを事例を用いて、標準を守らないとどういった不具合があるのか?そこまで教育していない。
品質管理のポイントを「見える化」する。
1、のメンテは言うのは簡単ですが、実際には難しい。何かトラブルが有る度に問題になり、嫌な気持ちになりがちです。
作業標準書は、新人に作業を教えるのに必要ですが、実際の作業時に、都度、標準書でチェックするでしょうか?しないですよね。
作業方法に関しては割愛し、品質を作りこむ上で外せない物のみ、見えるようにしておくのが大切です。
■写真/作業方法での見える化
2、も文章なので、十分伝わらない。実作業の際に注意喚起を目的として、写真に管理項目を入れ込んだ資料を作り、現場の見えるところに掲示する方法がお勧めです。
■チェックシートで見える化
チェックシートでポイントを確認してもらうことも大切です。
標準書よりは現場で活用されやすく、必要な情報もまとまっているので作業標準書よりはメンテしやすいです。
そうは言っても、標準書同様、納得性が無いと、信頼性が薄れ、チェックだけするようになります。
そうなると、二重チェックだ、等、話がおかしな方向に進みます。また、何かあるとチェック項目が増えて行くことになり、本来はチェックシートがあって有難いとなるべき物が、現場には不評になりがちです。
従って、次の対策が非常に大切になります。
標準作業を守らないとどういった不具合が発生するのか十分に納得してもらう。
私の経験を紹介します。
ガラスの梱包、開梱作業時に、色々なものがガラスに接触してガラスが割れることが分かっていました。ただ、現場で作業する方と話をしても、そんな物はぶつけない。疑うのか?といった感じになります。
そこで、色々な材料を持ってきて、ガラスに軽く接触してもらって、ガラスが割れるか割れないか、実感してもらいました。
あまりガラスのわれにつながるようなイメージのないプラスチック段ボールなども、角が当たると、薄い硝子の場合簡単言われます。プラスチックの定規でも同じです。
そういったことを経験していただいたおかげて、具体的な作業方法の改善が進み、新人の教育にも「割れ体感」として実施してもらうまでになりました。
納得いただければ自然と改善案も出ますし、チェックシートもなくても気を付けてもらえます。実感していただくことの大切さを身に染みて感じました。
朝礼、終礼を活用する
朝礼の時に、標準作業を守る、と宣言してもらう。終礼の時に、標準作業が守れたか相互確認を行うなども良い方法かと思います。
行動科学を応用する
- 目標は出来るだけ具体的に、観測できるように数値化する
- 大きな目標は達成できる小さな目標に切り分ける。
- 目標、パフォーマンスに直結する望ましい行動を標準行動とする。
- 標準行動の実施状況を測定する。
- 測定結果をFeed Backする。(グラフなどの見える化)
- 本人が望むものをすぐに与える。(ご褒美)、で行動を強化する。
- ご褒美は初めは頻繁に行うのが良いが、ある程度たてば、ポイント、ポイントで行う。
短期間で組織が変わる行動科学マネジメント 石田淳 ダイヤモンド出版 より、筆者が要約
人間は、行動を行う事で、何か望ましい事が起こると、その行動が強化されると言われています。その考えを標準作業を浸透させるのにも応用できると思います。
正しいと思って実施したミスの対策
これに関しては、失敗学実践編(日科技連出版社、浜口哲也氏・平山貴之氏)をお勧めしま
す。以下はこの本からの引用になります。
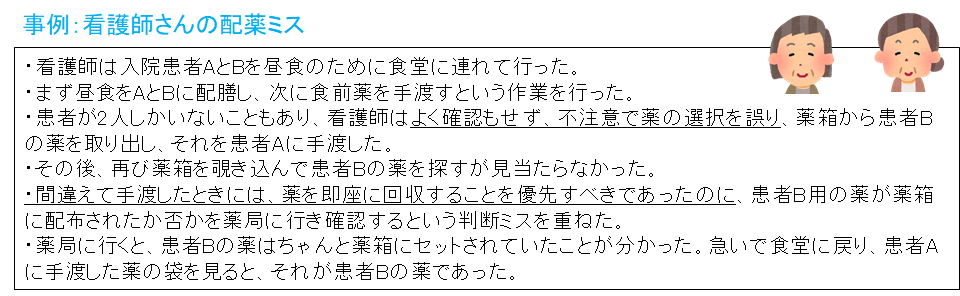
対策は、薬を配るときはよく確認し、薬を間違えて手渡した時はすぐに薬を回収するよう、再度関係者に教育を行った
これで大丈夫か?
動機的原因:なぜその行為が正しいと考えたか?
その動機的な原因は
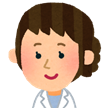
- 「Bさんですね」って聞いたら「はい」って言ったんだもん。
- お顔をみてBさんだと思ったんだもん。
であった。
つまり、
動機的な原因は言い訳であり、だって○○だったんだもん。といったフレーズがしっくりくるかどうかが大切。この言葉がしっくりこないものは、動機的原因にならない。
動機的原因は本人に確認するしかない。ただし、その行為が正しいと思ったことを認めた上で、どうしてそう思ったのかヒヤリングする必要がある。
■「否定形は結果論」
原因に否定形の事が原因として書かれているのは、すべて、対策を先に考え、それを反転して原因としているだけ。マニュアル、標準書が無かった。ルールが決められていなかった。不明確な指示だった等。
そもそも、逆を考えてみれば分かります。
標準書が有ればそのミスはなかったと言えますか?
何か思う所が有って、その行動をとったわけですから、問題になると思わなかった。などは原因になるはずです。問題になると思ったら行動しなかったわけですから。。。。。。
次はどうして問題になると思わなかったの?です。以前もそうやっていたから、等、色々出てくると思います。
以前もそうしていたのなら、今回と以前と何が違っていたのか、等、色々調べると問題点が色々見えてくると思います。
「上位概念に上れ」動機的な原因から失敗のカラクリ(上位概念へ)
事例から結局、どういうことかを考え、原因を一般化して「失敗のカラクリ」を導き出す。そのためには、事例レベルの上位概念(中位概念)今回のワナ、その更なる上位概念「失敗のカラクリ」を考える。
上位概念化するにはつまり、結局どういうこと?例えば、他は?で概念の上下動を行う。「対比・類似・因果」、「正・反・合」が大切。
もう少し具体的には下記の記事を参照ください
薬を間違えて配った例では
- 今回のワナ:ベッドから離れたらもはや患者識別不能
- 失敗のカラクリ:「本体とラベルを分離したら本体識別不能」の法則
成功のカラクリ
失敗のカラクリから成功のカラクリを導き出す。成功のカラクリ:本体にラベルをつけろ。
未然防止
成功のカラクリを各事例に展開し、未然防止に。
まとめ
- 知識、技能が不足している場合、
- 教育、訓練を行う。
- 習熟度を判断するシステムを作る。
- 標準作業よりも自分の判断を優先させた場合。
- 標準書を守らないとどういったトラブルが発生するか、誘発するか教育する。
- 標準書のメンテナンスは出来ているか確認し対応する。
- 品質管理のポイントは見える化出来ているか確認し対応する。
- 正しいと思って実施したミス動機的な原因を探り、
- 上位概念化し失敗のカラクリを探る。失敗のカラクリから成功のカラクリを見つけ出し、各々の事例に展開することで未然防止を図る。
コメント