品質改善は不具合の原因を追究し対策を打ちます。品質を確保するためには、コストアップも生産効率ダウンも望ましくはないですが避けられない場合が有ります。
しかし、IEはムダを排除し、生産効率、コスト削減を探るものです。コストアップ、生産効率ダウンになるような対策は本末転倒です。全体最適、未来最適などの問題の捉え方、また、現場のモチベーションアップが非常に大切になってきます。
IEとは?
同じ品質をより効率的に作る工程設計、ムダ、ムラ、ムリをなくし、生産効率とコスト低減を追究するための分析手法や改善手法の事です。
ムリ、ムラ、ムリをもう少し詳しく説明すると以下のようになります。
- 工程、作業、動作のムダ
- 付加価値を伴わない作業はムダ
- 作りすぎ、不良、手直し、運搬、在庫、待ち時間、
- 工程の流れ、作業の速度のムラ
- 待ちや突発的な停止(故障)
- 製品品質の大きなバラツキ
- ベースの乱れは、災害や不良品発生の原因ともなる
- ムリなやり方、使い方
- 無理をする原因をなくす。(技能訓練は重要)
- 匠の技はムリな動作が無く、肩に力も入っていない、匠の仕事は早い
工程、作業、動作のムダは人だけではありません。例えば加工機で考えると、自動機でも、加工していない時間は無駄な時間です。
IE問題の捉え方
部分最適と全体最適
現状を色々な分析手法を用いて分析したり、データーで整理し、モノの流れに着目してみるとムリ、ムダ、ムラが見えてきますが、すぐに改善を進めると後工程、あるいは前工程にとっては、改悪となる場合が有ります。
ある工程の生産性を上げるのは良い事ですが、他に生産能力の低い工程があれば、処理しきれない在庫が増えるだけで、製品になるまでの生産性は逆に悪化するようなことも考えられます。
前工程から見れば、必要以上に生産量を増やす必要があるので、無駄な作業が出てくるでしょう。
ネックとなる工程を探すことが大切になります。
物が停滞している所が怪しいとなります。工程毎のリードタイムを下のように生産能力表として比較すれば、生産性の低い工程が分かります。
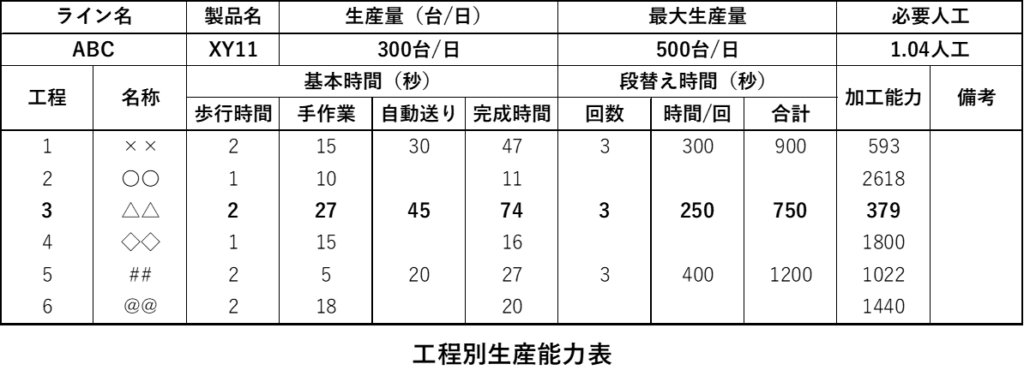
例えば、上の表のような工程で、500台/日の生産をしようと思ったら、能力が500に満たない3工程の改善を進めなければなりません。
稼働時間が8時間(28,800秒)なので、500個作ろうと思ったら、段替え時間の750秒を引いた(28800-750)/500秒で完成させる必要が有ります。計算すると56秒です。
現在、74秒かかっていますから18秒、改善しなければなりません。
生産性の低い工程の分析を集中的に進め改善を進める必要が有ります。あるネック工程の改善が進めば、別の工程がネックになります。
現場を元気にする楽しい改善7ステップ 越前行夫 日刊工業新聞社 より
現在最適と将来最適
お金もかからず、すぐに実施できる事なら、すぐに実施すれば良いと思いますが、その改善がいつまでもつのか?を考える必要が有ります。
生産量が減っていく品種の改善を進めるよりは、今後生産量が増え、主力になってくる品種の改善を進める方が効果的なのは明らかです。
改善の有効期間がどのくらいなのかを考える必要が出て来ます。
IE問題の対策
ECRS、作業をやめられないか?
- E limnate:なくせないか?
- C ombine:一緒にしてしまえないか?
- R earange:再構成したらよくなるか?
- S implify:簡素化できないか?
E:作業を改善すると考えるよりも、まずはやめられないか、と考えるのが最初です。改善ありきで考えると失敗することも多々あります。
そもそも、お金を発生しない工程は作業をなくすのが一番の改善です。そもそも、その作業をやめて、どういった問題が発生するか?後工程、お客様も含めて確認すべきです。
C:一緒に出来ないか?二つ以上の作業を同時に出来ればそれだけ効率的になリます。装置を止める必要のある内段取りを極小化し、外段取りを増やす必要があります。
外段取りの基本は5S、必要なものがすぐ手元にある事、必要な工具をキャスターに載せて、物を探したり、取りに歩く時間をなくすなどの工夫が必要です。装置を止めないと出来ない段取りと、止めなくても出来る事は何かを特定することが大切になります。
また、往々にして多いのが、段取り替えに伴う調整、その確認にかかる時間です。調整が必要な原因を突き止め、確認はその場で確認できるように工夫する必要が有ります。
R:順番を入れ替えると上手く行ったりしないか?という事です。折角加工しても、その後の加工で精度を悪化させるのは無駄になります。穴あけ加工してから溶接するよりは可能なら溶接してから加工した方が良い等です。
S:は簡素化、作業そのものや製品そのものを簡素化するという事。
ECRSは順番も大切で、E→C→R、そして最後にSを検討するのが大切となります。
装置導入、自動化の注意点
前提条件はすぐに崩れる。
生産量に合わせて装置を導入するのは必要ですが、安易に装置導入を検討するのは良くありません。実際には購入しなければならないのですが、その際、そもそも、生産量はどのくらい、品種構成、場所、等、色々な前提条件を付けて装置仕様なり台数なり決めて行きます。前提が無いと細かな所は決められません。
しかし、工程の場合、お客様の都合、材料供給メーカーの都合、需給状況(急激に生産が増えた、減った)工程のトラブル、等々、によって待ったなしの状況に追い込まれます。
ある主力製品の工程改善を進め、段取り替え時間を短縮し時間短縮を図ったとして、後工程でトラブルが発生し、ラインバランスが崩れるため、生産調整しなければならなくなるとか、管理業務を効率化するためにソフトを導入したが、当初の要件が合わなくなり、逆にインプット作業が増え効率が悪くなったなどです。
そのためには、前提条件の精度を高める事も大切ですが、各工程のムリ、ムダ、ムラ、を取り除き生産性を上げ、トラブルにも対応できるように無駄のない、筋肉質な工程にしておく事が結局大切になると思います。
装置導入の際の注意ポイント
清掃しやすい、メンテナンスしやすい、段替えしやすい、などは実際に使ってみないと分からないところが有る。安易に装置化するのではなく、十分に改善活動を行ったうえで装置化するのが望ましいです。
ムダを突き止め改善しておかないと、ムダを装置化することになり小回りが利かなくなります。
理想は一個流しで以下に短時間で生産できるかである。機械とはいえ、無駄な動き(エアーカット、空転など)は減らさなければなりません。
不要な機能は極力除いて、小型化、を図ることも大切であるが、専用装置になると転用が利かなくなるので、専用装置は避けるべきです。
初めから完全な自動化を狙うと上手く行かない事が多いです。加工はものすごく早くできても、往々にして製品の脱着で上手く行かない事が多いです。
出来ればプロト機で十分検証してから購入するのが望ましいです。装置を入れても、調整のために人が張り付いたり、稼働率が上がらないのでは意味が有りません。
またすべて自動で動くことを前提にするとトラブルが発生した時に身動きが取れなくなります。いざという時の代替手段や、スペース的な遊びも考えう必要が有ります。
装置のスケールアップについて
プロセス設計の場合、得てして、装置のスケールアップに伴い、空間的不均一、時間的不均一が原因で品質そのものが一定にならない場合がある。特に化学変化をともなったり、攪拌や混合を伴うものは注意が必要になる。開発事項になるので品質工学の手法を使ったりして、マージン評価を十分に行う事が大切になります。
人と組織の問題
改善を進めるにあたっては、現場の改善が基本です。まずは、現場のメンバーがやりがいを持って進めるられる状況にすることが非常に大切です。
なぜなら、お金を生み出しているのは現場であり、その改善を進めないと、それこそ、ムリ、ムダ、ムラを誘発することになります。
現場の問題を改善するのは現場であり、スタッフはその為の資源的・時間的余裕を持たせ、モチベーションを引き出すのがスタッフの仕事です。
以下、IE問題の基礎 川瀬武志 日刊工業新聞社 からの引用になります。
- ラインのすべてのメンバーが自らの努力と責任によって改善活動を行う。その為の資源的・時間的余裕を持たせるのがスタッフの仕事である。
- 手法やアプローチの提供および、教育、訓練に関する支援を行う。勤務時間内で改善活動を行う時間を確保するのがスタッフの仕事である。
- 継続的な改善が可能である
- すべての問題について、誰かが考えており、漏れがない。
- 処理される問題の数が飛躍的に向上するので問題解決能力が飛躍的に向上する。
- 変化に対する抵抗が少ない
書籍では、合計16個のメリットがあげられていますが、私が感じた、大きなメリットを4個紹介しました。
以下の記事で詳細を紹介しています。参照していただけると有難いです。
まとめ
- IEとは工程のムリ、ムダ、ムラ、をなくし、生産効率を上げ、コストダウンを図る分析、改善手法の事。
- 対策講じることで改悪にならないように、部分最適ではなく全体最適を図り、今だけではなく、将来にも目を向け、改善の有効期間を見積もる事が大切になる。
- 対策はまず、止められないか、を真っ先に考えるのが基本、改善有りきでは失敗する。
- 装置化の前のムリ、ムダ、ムラを排除しておく事が大切
- 最初から完全な装置化を目指すにはリスクが高い。いざ追う時の代替、遊びは必要
- 現場の改善が基本、ラインのすべてのメンバーが自らの努力と責任によって改善活動を行う事で、継続的な漏れの無い改善活動が可能になる。
- 現場の問題を改善するのは現場であり、スタッフはその為の資源的・時間的余裕を持たせるのがスタッフの仕事である。
- 現場を元気にする楽しい改善7ステップ 越前行夫 日刊工業新聞社
- IE問題の基礎 川瀬武志 日刊工業新聞社
コメント