- 原因が明確になっても対策を立てるのは簡単ではありません。原因同様、物理的な問題。人の問題、業務上の問題で分けて考えることが大切です。
- 対策は原因除去、頻度を下げる、流出防止の3点で考える事が大切です。
- 実施に当たっては社内でルール化して確実に実施する事が大切です。
- 効果の検証では実際の効果だけでなく、暫定対策の見直しや、思わぬ副作用(悪影響)が無いか確認する事も大切になります。
対策の検討
物理化学的な不具合の対策
暫定対策
すぐに出来る事。流出防止、
暫定対策は応急処置ですので、一番大切な事はすぐに出来る事と、流出防止です。けがをして血を流している時はまず、血を止めるのに包袋等で真っ先に処理しましょう。
生産性が一時的に落ちたり、検査を厳しめに実施しなければならなかったりしますが、まずは、流出防止を実施し、確実に品質を確保させることが大切になります。
ただし、上記はクレームのような緊急性の高い課題になります。暫定対策に時間をかけるよりも恒久対策をじっくり考える事が大切な場合もあります。何が何でも、まずは暫定対策と考える必要はありません。
また、暫定対策は本来、恒久対策が出来れば、見直すべきですが、一旦、お客様に提案すると、見直すのが難しくなります。
お客様に報告すべき暫定対策と、社内でクローズできる暫定対策と分けて考える事も大切になります。
恒久対策
原因が分かったとして、以下の3点で考える必要があります。
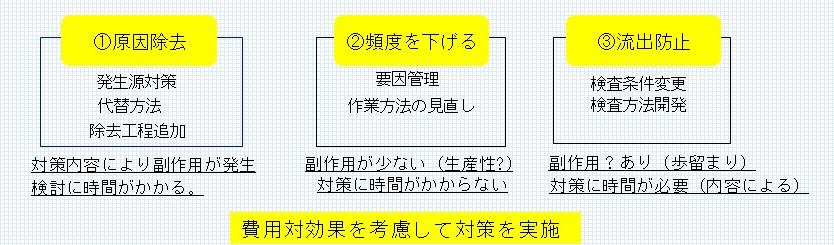
①原因除去
原因が明確になった場合、真っ先に考えるのは発生源対策でしょう。ただ、副作用は常に考える必要はあります。
例えば、構造体である部分が強度が低いことが分かった。しかし、補強して強度アップを測るとその分、他の所にしわ寄せが行って別の不具合が発生する。
例えば、製品にある汚れがついていた。その汚れは加工工程で使う材料であったので、その材料を変更したところ、やはり加工性で別の問題が発生した。
また、対策に非常にお金がかかったり、本質過ぎて対策が取れない場合もあります。
②頻度を下げる
比較的多く用いられる方法かと思います。
例えば、製品に汚れがついていて、その汚れはある機械に使っているオイルだったので、アクリル板で飛散防止処置をとった。等、
③流出防止
普通は検査時間アップや歩留まり低下につながりますので、よりピンポイントで検査できるよう、場合によっては検査方法自体を見直す必要も出て来ます。それ程簡簡単ではありません。
対策を決めるには?
原因は明確になったとして、いきなり具体的な対策を考えると他に目が行かなくなります。決めつけはいけません。原因除去、頻度を下げる、流失防止の点で考えられるアイデアを出来るだけブレストなどで数多く出し、後で同じようなものをまとめて行くブレスト+親和図法が適していると思います。
そのうえで、費用対効果/リスク評価を行い対策を決めて行くしかないと思います。
人に起因するトラブル、品質問題の対策
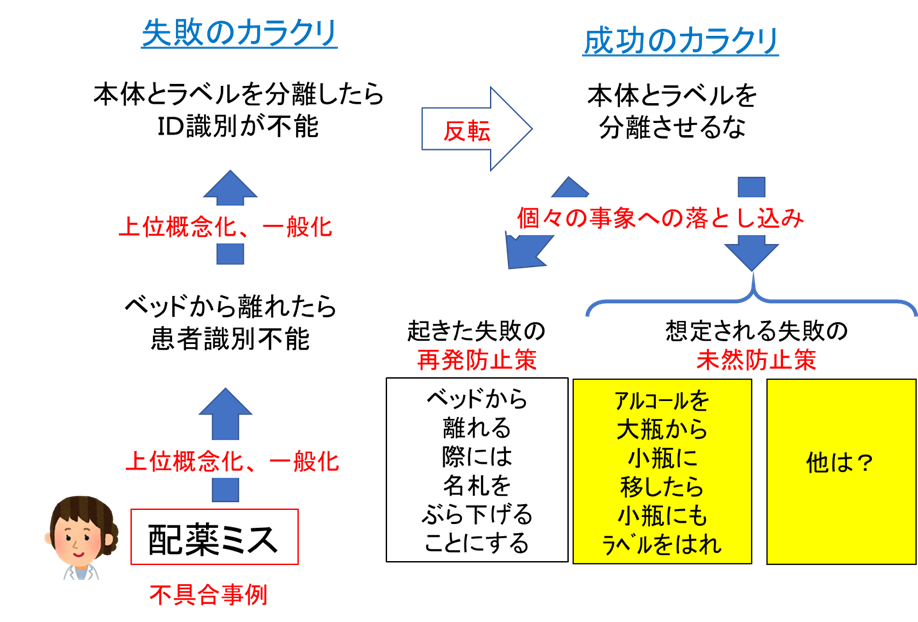
人が行った行動の動機から失敗のカラクリを、反転させて「成功のカラクリ」(対策)を導き出すことになります。
詳細は失敗学実践編、濱口哲也・平山貴之 日科技連を読んでいただくか、以下の記事を参照ください。
業務上の問題に対する対策
新QC7つ道具の系統図法を用いて対策を決めると良いでしょう。
目的から手段に展開して行く方式で連関図法を用いて洗い出した主要因を解決する事を目的とし、具体的な手段にまで展開して行く方式です。
原因を特定したら、その原因を防ぐ(あるいは取り除く、解決する)のを目的とし、展開して行く事になります。
系統図法に関しては、下記の図やサイトが分かりやすいと思いました。良ければ参照ください。
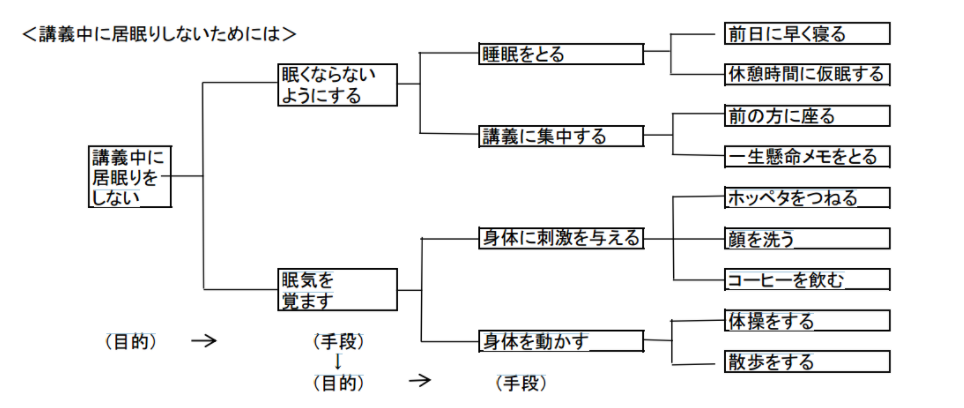
そもそも原因を追究するには?
原因を追究する手法は以下の記事を参照願います。ロジックツリーを使ったMECEな展開、「なぜなぜ分析」による深堀、連関図法を用いた要因の関連性調査、主要因の推定。検証が大切になります。
- 原因追及
- ロジックツリーを使ったMECEな展開、
- 「なぜなぜ分析」による深堀、
- 連関図法を用いた要因の関連性調査、主要因の推定。検証
- 対策立案
- 系統図法を用いて原因を解決する為の具体的な手段まで展開
実施と効果の検証
実施
対策を決めたら計画を立てて粛々と実施して行く事になります。
- 物理的準備、必要な道具やツールなど
- 環境面の整備、必要な対策を実施するにあたって必要な環境整備
- 人の整備、担当者、実施者の選定、必要に応じて教育、確実な社内承認
- 初品流動時にどういった評価を行い、どういった処置を行うか?その判断基準は何か?
特に4については、4M変更や初品流動評価等、効果を確認する方法を社内ルールとして定め、フォローして行く事が大切になります。
効果の確認
クレーム関係であれば、有りがちなのがいったん沈静化してしまうと何となくそれで良しとし、一連の対策の結果がどうだったのか検証しないままになる事が多々あります。
不具合は解消されたものの、実は思わぬ副作用で他の品質に悪い結果を与えていた。等という事もあります。また、想定していたよりも生産性が悪化した等の事もありがちです。
実施した後の効果の確認は想定していなかったマイナスの要因が無かったか、効果はあったのか?検証しましょう。
また、暫定対策を行った後、恒久対策を実施したものの暫定対策だけが残ったりします。暫定対策は恒久対策を展開したら基本、辞めるべきです。しっかりレビューしましょう。
まとめ
- 対策
- 物理化学的な不具合の暫定対策は、すぐに出来る事。流出防止が大切
- 暫定対策は応急処置なので恒久対策が出来たら見直し(基本廃止)が必要
- お客様に報告する暫定処置は見直しがしにくくなるので注意が必要
- 恒久対策は、費用対効果を検討の上、原因除去、頻度低減、流出防止の3点で考える。
- 人に起因する問題の対策は、行動の動機から失敗のカラクリを導き、反転させた成功のカラクリ(対策)を導き出す。
- 業務上の問題の対策は、連関図法などで明確にした主要因を解決することを目的とし、手段にまで展開する
- 実施と効果の検証
- 社内でルール化して確実に実施する事が大切。
- 効果の検証では実際の効果だけでなく、暫定対策の見直しや、思わぬ副作用(悪影響)が無いか確認する事も大切。
コメント