なぜ、「見える化」IE手法が何故大切か?
製造現場の落とし穴
長年、同じ職場にいると外部環境の変化に疎く、標準書通りにやっているから問題なしと考えがちになります。
また、現状のやり方を変えることに抵抗が有ったり、量や質のバラツキをやむ負えない。これが正常と考えてしまいがちです。
この落とし穴に陥らないためにはどうするか?
♦上司の適切な指導
上司は、お客様の状況、社内の方針などから、将来も見通して、問題意識を現場に持たせる必要が有ります。これは上司の大切な役割です。
しかし、実際の改善策は現場に考え、実施してもらう事が大切です。
上司の仕事は、現場が考え、実施できるように、改善の時間を確保し、教育や訓練を通じて、改善策を考えられるようにするのが大切です。
自分たちで考えて実施して行くので変わって行く事の抵抗は有りません。
そうやって、成功体験を重ねて行く事で、現場にも活気があふれ、自主的な改善が進む良い循環に入っていき、改善意識が高まります。
記事にまとめていますので良ければ参照願います。
♦見える化
個人個人が個別に気が付いたムダ、ムラ、ムリを改善して行くのはそれはそれで大切ですが、大きな効果は期待できません。
改善を進めるにあたっては、部分最適ではなく、全体最適を考える必要が有ります。その為には、全体をまずは俯瞰したうえで、ネックとなる工程を見つけ出し、詳細に実態を観察、分析する事が大切になります。
また現状が見えるようになるので、改善に対して関係者の協力も得やすくなるといった効果が有ります。
それらの手法として、既に確立された手法(IEの手法)が有りますので紹介して行きます。
IEは現状を分析し、見える化することで、説得力も出てくるため、問題点を炙り出すだけでなく、関係者の協力も得やすくなる。
◆分析結果はメンバー全員で共有し、議論する
分析結果はメンバー全員で共有し議論し行動に移さないと宝の持ち腐れになります。当たり前ですが、とても重要な事です。
ムダ、ムラ、ムリについて
ムダ、ムラ、ムリについて、改めて定義すると以下のようになります。
- 工程、作業、動作のムダ
- 付加価値を伴わない作業はムダ
- 作りすぎ、不良、手直し、運搬、在庫、待ち時間、
- 工程の流れ、作業の速度のムラ
- 待ちや突発的な停止(故障)
- 製品品質の大きなバラツキ
- ベースの乱れは、災害や不良品発生の原因ともなる
- ムリなやり方、使い方
- 無理をする原因をなくす。(技能訓練は重要)
- 匠の技はムリな動作が無く、肩に力も入っていない、匠の仕事は早い
IEの分析手法
分析をするには標準化されている事が前提
色々なIEの手法を使って分析を進めるにしても、分析する作業自体が標準化していないと、分析してもばらつきのどの範囲なのか不明です。
なので、まずは、作業を標準化しておく事が必要です、標準化するにおいては、どういった作業が必要で一番良い方法なのか、不要な作業は何なのが、作業の整理整頓をしておく事が大切です。
人に余裕が有り、作業員の数も多くないのであれば、作業員全員の作業分析を行ったり、ビデオにとって比較する。という事も可能です。
工程分析
全体としてどの工程を流れているのか一旦整理する必要が有ります。
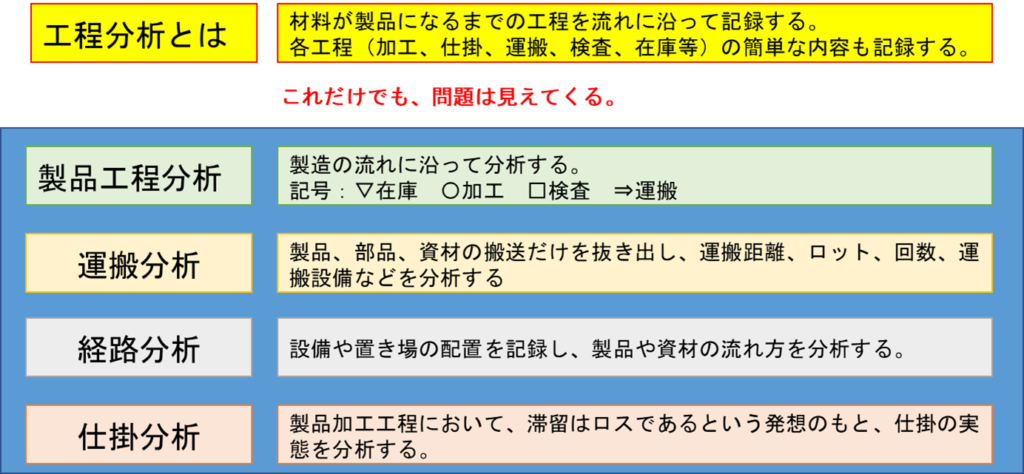
工程分析も、製品工程分析と、運搬や経路に特化して分析するなどが有ります。搬送や、経路だけでなく、個別に特化しても良いです。この記事では製品工程分析で例を紹介します。
仕掛分析は他の工程分析とは趣が違っていて、流動数曲線と呼ばれる生産量が計画に対して実績がどう推移しているか示したもので、リードタイムや仕掛品の在庫量を大まかに把握する方式です。
製品工程分析
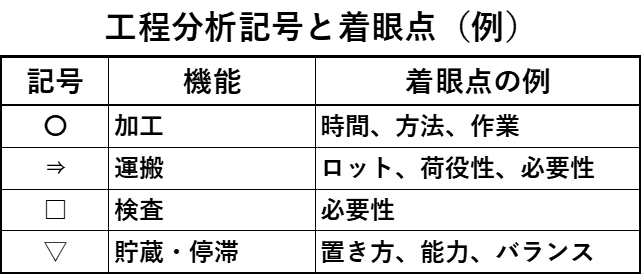
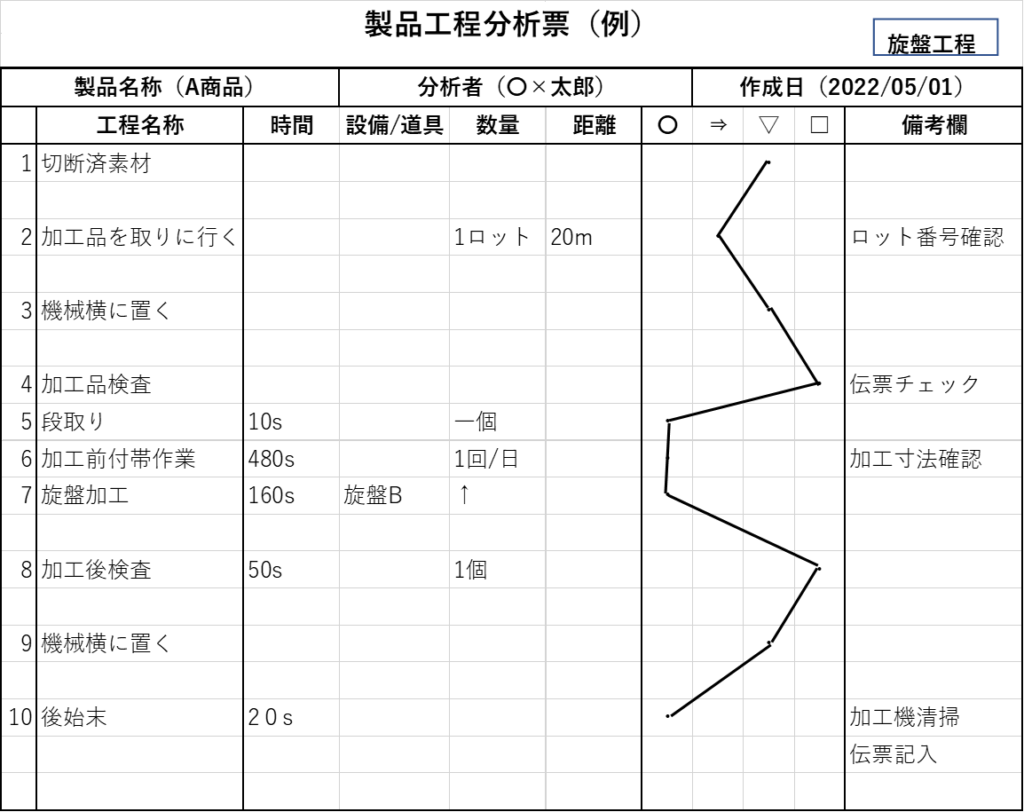
運搬分析
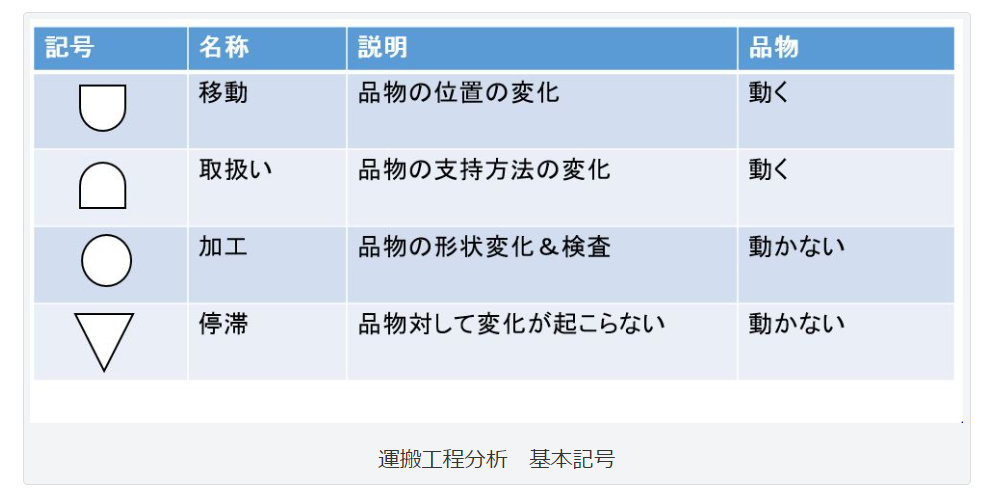
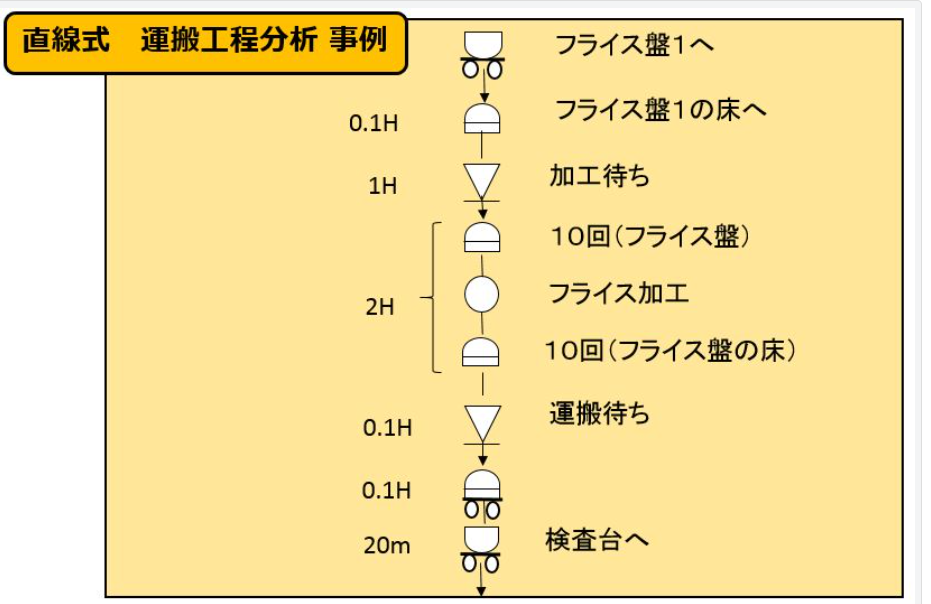
経路分析
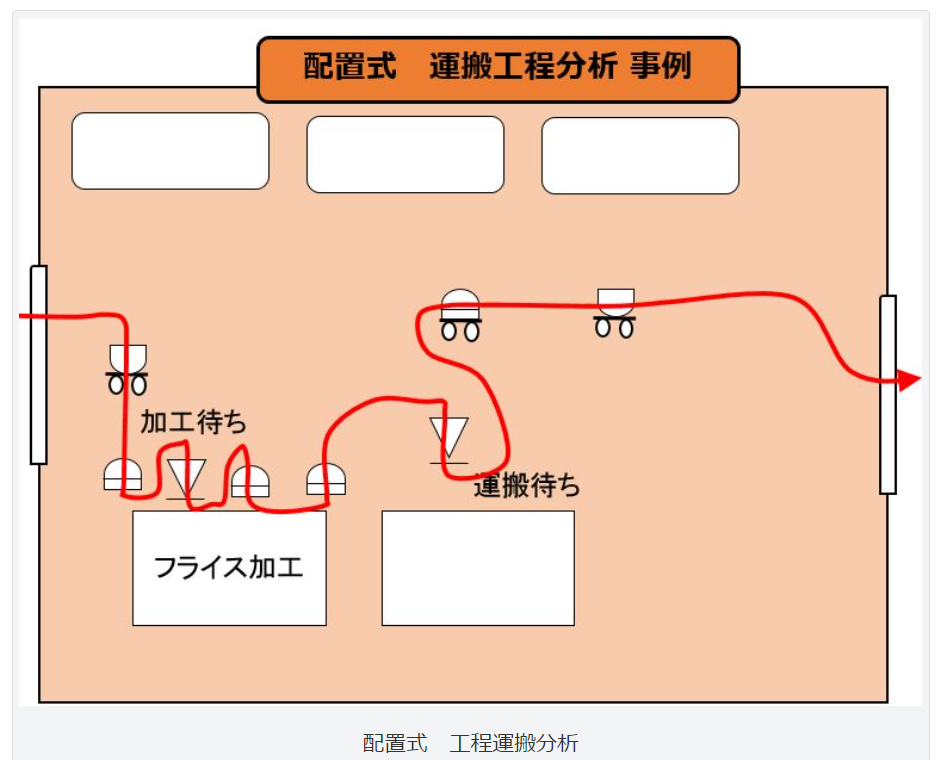
仕掛分析
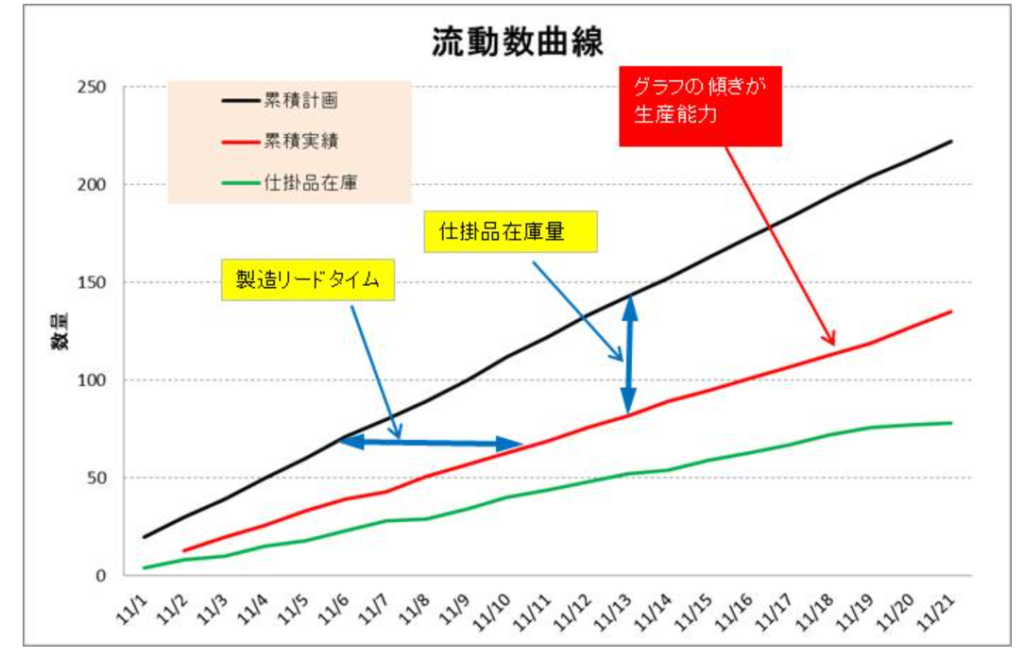
黒い線が累積計画数で、赤い線が累積計画数です。
- 製造リードタイムは、日数の差なので、黒い線と赤い線の横の長さに当たります。
- 仕掛品在庫は、数量の差なので、黒い線と赤い線の縦の長さに当たります。
工程は全体を整理して、改めて確認できるのが利点ですが、実際に改善しようと思ったら、ネックとなる工程を選び出し、より詳細に、作業や時間を分析する必要が出て来ます。
稼働分析
稼働の状態を調べる観測手法です。
♦連続観察法
連続観察法は一人が連続して観察する方法で、作業者に稼働状況を記録してもらう、あるいは、工程が限られていれば、第3者が観測する事も可能でしょう。
♦瞬間観察法、ワークサンプリング方
しかし、工程が多くなったり、装置も多いと、人が張り付いて観測したり、作業者に記録してもらうのも難しくなります。
その際には、数日から数十日の間、ランダムな時間に何回も瞬時に観察し、統計的な処理をして全体を推測する方法です。
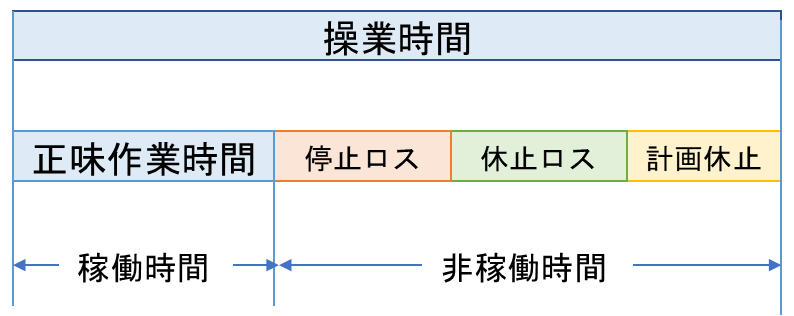
- 計画休止
- 定修、点検、始業Meeting など定められている休止時間
- 休止ロス
- 段取り時間、材料待ち、トラブル対応など、運転を阻害する休止時間
- 停止ロス
- 材料確認、計測、空転、など設備が運転中に発生する休止時間
ネックとなる工程を探す。
物が停滞している所が怪しいとなります。工程毎のリードタイムを下のように生産能力表として比較すれば、生産性の低い工程が分かります。
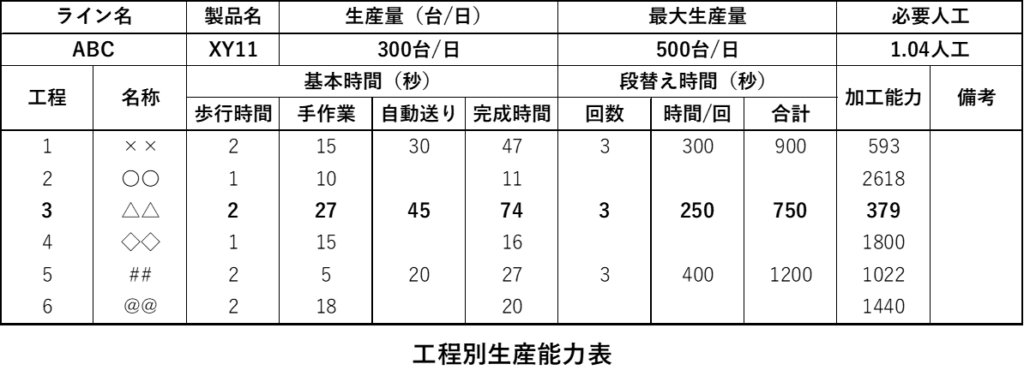
例えば、上の表のような工程で、500台/日の生産をしようと思ったら、能力が500に満たない3工程の改善を進めなければなりません。
稼働時間が8時間(28,800秒)なので、500個作ろうと思ったら、段替え時間の750秒を引いた(28800-750)/500秒で完成させる必要が有ります。計算すると56秒です。
現在、74秒かかっていますから18秒、改善しなければなりません。
生産性の低い工程の分析を集中的に進め改善を進める必要が有ります。あるネック工程の改善が進めば、別の工程がネックになります。
現場を元気にする楽しい改善7ステップ 越前行夫 日刊工業新聞社 より
作業分析、時間分析
ネックとなる工程の作業、時間を詳細に分析する手法です。
♦作業分析
問題の工程に絞って、その工程での作業者の作業内容を克明に分析する。そのことで、作業者の動きのムダ、手順の誤りが浮かび上がってくる
♦動作分析
作業分析の結果浮かび上がった問題の作業について、更に細かい動作を記録し、視線や両手の動き、部品の置く位置と動作の関係を記録する。ビデオ撮影も有効だと思います。
♦時間分析
工程全体の時間観察や問題工程に絞って時間観測を行う。ストップウォッチなどで作業者の作業時間、機械の加工時間、段取り替え時間などを記録する。
連合作業分析
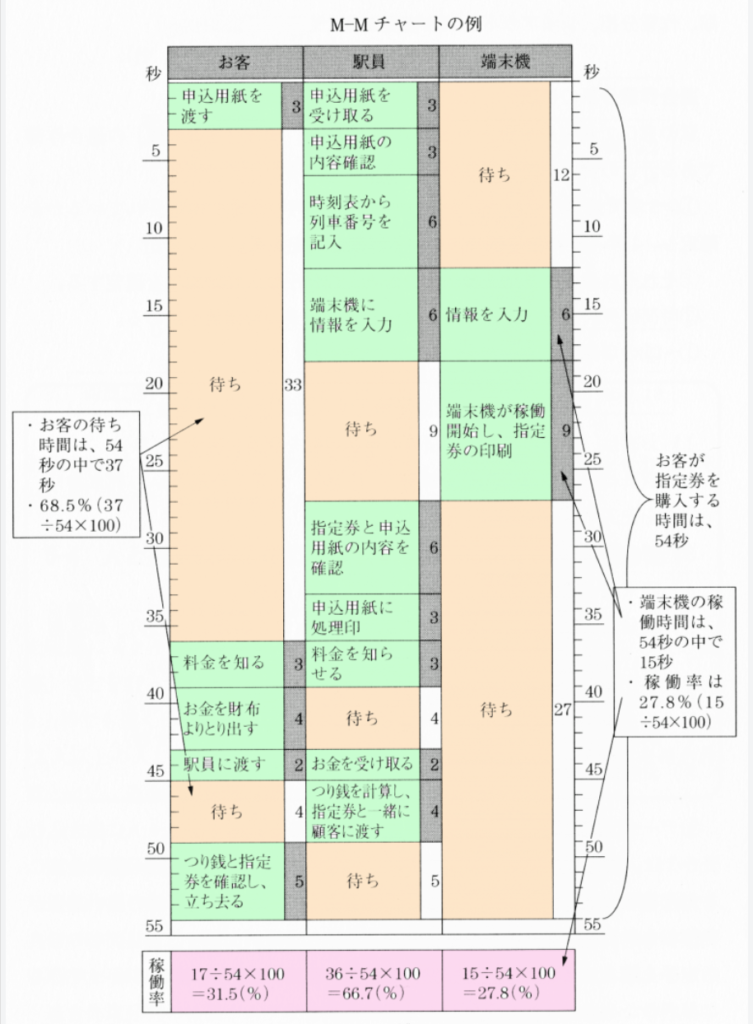
右の図は、M-Mチャートとは?|マンーマシンチャート | 改善.net (kaizen1.net)に記載されていた、駅の窓口で指定券を購入する場合のM-Mチャートです。
工程の現状分析として、例えば右に示した図はM-Mチャートと呼ばれ、人と、機械の稼働状況、有効な仕事をどのくらいしているかが分かるチャートが良く使われます。
連合作業分析とも呼ばれるようです。
コストダウンの観点に立てば、待ち時間など直接お金を生み出さない準備時間等を減らすという事になります。
右のM-Mチャートであれば駅員さんは実質的な価値を生み出さないので、お客様に端末機を扱ってもらうといった事が考えられます。
IoT技術、BI技術の活用
最近は、スマートロガーと呼ばれるように作業計測が簡単にできるように成ったり、BIと呼ばれるように、多くのデータを簡単に「見える化」出来るような技術も進んでいます。
今後も新しいものがどんどん出てくると思います。お金と時間が許せば、展示会に言ってみるのも良いと思います。
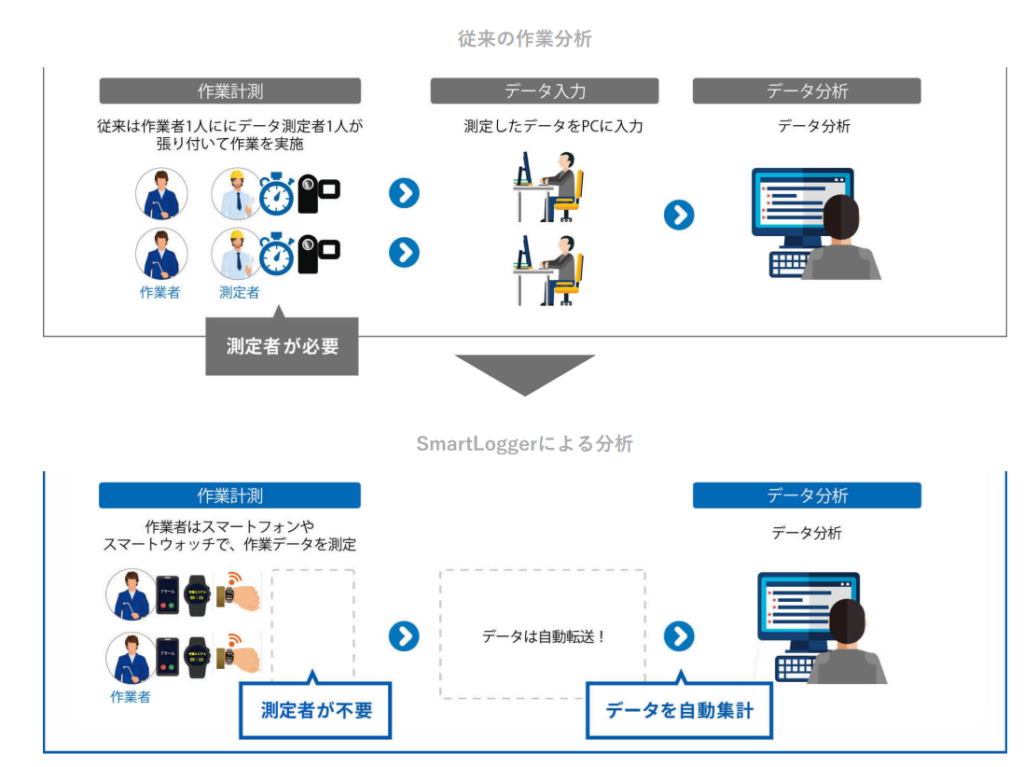
まとめ
- 改善を進めるには全体を一旦整理し、問題のある工程を更に観察、分析する事が必要
- IEは現状を分析し、見える化することで、説得力も出てくるため、問題点を炙り出すだけでなく、関係者の協力も得やすくなる。
- IE手法は 製品工程分析、運搬分析、経路分析、仕掛分析、稼働分析、作業分析、時間分析、連合作業分析などが有る
- IoTやBIと言われる最新情報はすぐに使える情報が多く、展示会などで情報を集める事も大切
コメント