私が改めて言うまでもなく、機械は必ず壊れます。人はミスもしますし予期せぬ行動もとります。完全な管理システムもないと思った方が良いでしょう。
人は予期せぬ行動をとる、はあまり言われていないと思いますが、すべてのケースを想定は出来ません。状況や環境によっては「なんであんなことしたんだろう?」と思う事もあるでしょうし、病気で意識を失うような場合もあるでしょう。
機械は必ず壊れる、人はミスをするのでそこを技術でカバーする必要が有ります。機械が壊れても、人がミスをしても危険が及ばないような技術を考える。というのが大切な考え方になります。
しかし、ミスを犯すと言いながら人間の教育や、管理システムなどの対策も非常に大切であって、結局トータルで考える必要が有ります。
また、リスクをゼロにすることは不可能です。許容できるリスクは何か?許容できないリスクは何か?を明確にして、許容できないリスクをゼロにすることが安全な状態とも言えます。
管理方法やルールなど組織で守る方法や人に対する教育などについてはお客様に考えるていただくことになりますが、設計側としては取扱説明書にて推奨する作業方法、残リスクを使用上の注意点等を記載、あるいは現物に表記する必要が出て来ます。
製品の安全設計
危険源、リスクの考え方
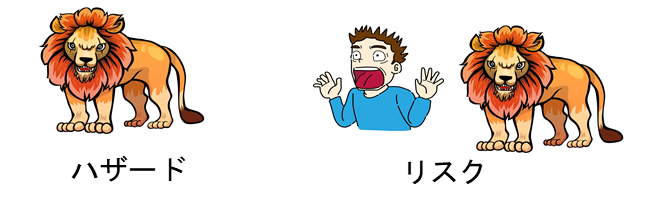
- ハザード(危険源):有害となりうる可能性のある現実
- リスク:有害な現実が起こる可能性。不確実性
危険源とは怪我の直接の原因となる現実です。例えば、ライオンが街中をうろついていたらいつ襲われるかわかりません。なので、ライオンは大きな危険源です。
しかし、ライオンがうろついているだけでは問題ありません。ライオンと人間が接触することで襲われる可能性が出てくるのです。
製品もそれだけでは危険ではありません。その製品を取り扱う事で場合によっては危険源ともなり得ます。なので、安全設計を考える上では、「その製品をどのように使うか」、これを明確にしておく必要が有ります。
お客様が必要される「使い勝手」から考えられる使用方法を明確にする
新製品の場合、お客様の使用状況をよく理解するのは実は簡単ではありません。基本、お客様はどのような使い方をするのか見せてくれません。製品もないのに作業の標準書もありません。お客様も、アイデアレベルの製品をどのように使うか?と聞かれても答えようがないでしょう。
なので、お客様から使い勝手に関する要求事項をよく聞いて設計に反映し、取り扱い方法を提案するといった具体的な話に持っていく事が大事になります。
すでに他社品あるいは自社品でも良いですが、実績が有る製品が有るのであれば、その違いを明確にしてお客様と協議するのが非常に大切になります。
使い勝手は操作性と理解しても良いですが、保護具を使う事の是非や、許容できる作業時間や作業人数など、お客様の許容範囲を確認しながら設計を進めて行くのが良いでしょう。
また、設計に必要なお客様のやりとりは極力営業を通さず、設計者が直接話をすることをお勧めします。
業務が忙しく時間が取れない。といった問題は有りますが、今はリモートでも十分画面越しに会話が出来ます。得られる情報は直接話すことではるかに多くなりますし、その場で議論が出来るので仕事は早く進みます。
一方で、その場である程度判断しないといけないところもあり、事前の社内打ち合わせも必要になります。慣れないうちは色々難しく感じるでしょうが場数をこなせばコツがつかめる(相手の言ってくることが読めるように)なってきます。
危険源の同定
使用方法が決まれば、危険源は何かを同定することになります。ISO12100 附属書B、表B.1に詳しいリストが記載されています。良ければそちらを参照ください。項目のみ下記に引用致します。
- 機械的危険源(電気を切っても油圧や慣性で動くものが有るので注意です。)
- 電気的危険源
- 熱的危険源
- 騒音による危険源
- 振動による危険源
- 放射により危険源
- 材料および物質による危険源
- 人間工学原則の無視により発生する危険源(ムリな姿勢による腰痛など)
- 滑り、つまずき、および墜落の危険源
- 機械が使用される環境に関連する危険源(温湿度、ほこりなど)
危険源はそれだけ考えても考えにくいです。リスクと合わせて、考える事が大切です。
「○○(危険源)が××なので、△△して、■■になる。」
の○○の部分を考えて行く事が大切になります。
リスクアセスメント
リスクアセスメントを行いリスク低減策を検討するのは製品設計でも同じです。
ただし、人の面。管理の面の対策を盛り込むのは実際に使ってもらう人の問題なので、製品の設計について対策できることを考えて行く事になります。
また、具体的に試作品もない段階でリスクアセスメントに力を入れても、製品として完成する時には仕様は大きく違ってくることは多々あります。
従って、洗い出した危険源とそのリスクから、考えられる重大事故を1~3件程度、被害状況と頻度を想定して選び対策を考える。といった簡易的なやり方で良いと思います。
量産前には妥当性確認のためにも、製品によってはリスクアセスメントをしっかり行いましょう。
一般的なリスクアセスメントは記事にしていますので良ければ参照してください。
設計時の製品安全対策(参考文献:入門テキスト安全学 向殿政男 東洋経済新聞社)
本質的安全設計対策
- 初めから危険源が無いように設計する。
- 危険源による危害の大きさを小さくするように設計する。
1,については、例えば毒性のある有機物を無毒の者に変えるとか、機器の空隙・間隔は指、腕、足、頭などが挟まれない幅にする、等です。
2,については人が触る可能性のある所はバリ取りや面取りを行う。あるいは、ぶつかる可能性のある所にはクッション材を貼る。等です。
フールプルーフ
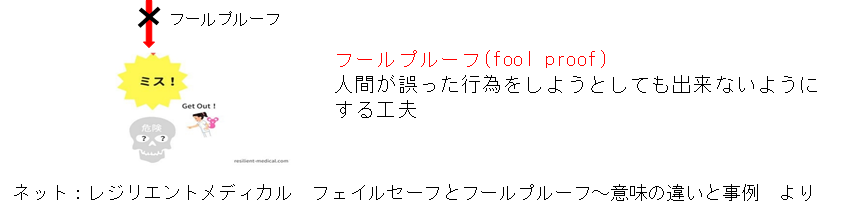
「ポカミス」対策として作業工程などに広く応用されています。
点滴のチューブの接続間違いを防ぐために接続口の形状を特定の物でなければ接続できないようにしたものなどが有名です。
製品設計の応用としてはインターロックが有名です。
ドアを閉めないと電源が入らない電子レンジ、ギアをパーキングに入れないとエンジンがかからない自動車、人間がいない時にしか動かないロボット、等です。
フェイルセーフ
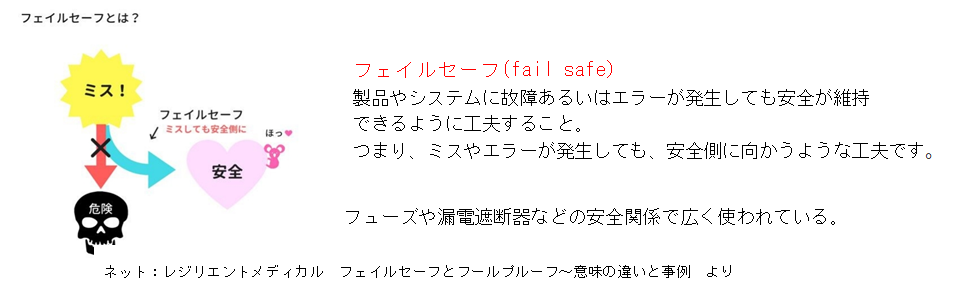
作業工程などへ応用するのであれば、ミスをしたら直ちに気が付く仕組み作り、として考えると色々考えられます。
製品設計としては、エラーが発生しても安全側に向かうように考える事です。一番、確実なのは装置を止める事なので「止まる技術」とも言えます。
例えば、人を射感知するセンサーでは、安全状態が確認出来るときだけ動くようなものを選びましょう。透過型のセンサーにすると壊れて信号が出なくても安全であるとの判断でロボットは動かなくなります。
一方、反射型のセンサーでは、人を感知した時にとめるようになっているので、壊れてもロボットは動きつ続けます。
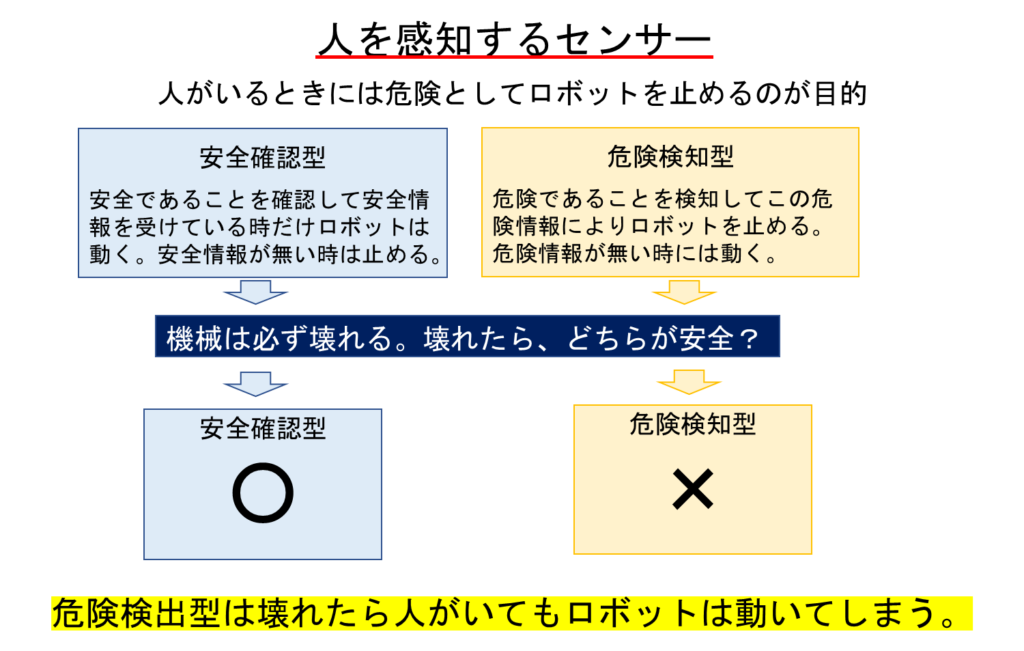
フォールトトレランス
故障が発生しても機能が保てるようにする事。冗長設計とも言われます。もしAが壊れたらBでカバーする。例えばスペアータイヤなどもそうでしょう。
センサーの数を増やして信頼度を上げたり、部品に壊れにくい物を採用する事も大切になります。システムで言えば複数台のシステムで稼働させることで負荷を分散させるなどもそうです。
まとめ
- 安全設計は機械は必ず壊れる。人は必ずミスをする。完全な管理システムは存在しない。
- 安全とは許容不可能なリスクがない状態である。
- 製品設計の安全対策は危険源とリスクを同定することが最初になる。
- 危険源とリスクを同定するには使用条件、使用環境を明確にする必要があるが、開発品の場合、お客様に確認しても回答はもらえない。
- お客様の「使い勝手」からくる要求事項から、設計側が使用条件、環境を提案する必要がある。また、既に実績が有る製品ならば、開発品と実績のある製品との違いに着目し、お客様と議論することが大切になる。
- 試作品が出来る前のリスクアセスメントは洗い出した危険源とそのリスクから、考えられる重大事故を1~3件程度、被害状況と頻度を想定して選び対策を考える。といった簡易的なやり方でも良い。
- 具体的な安全対策には①本質的安全設計対策、②フールプルーフ、③フェイルセーフ、④フォールトトランスの4っつの技術的ポイントで考えるのが良い。
コメント