QC工程表とは?
- QC工程表とは?
- 製品の品質がすべての工程にわたって、品質が管理がされていることを示す表
- 自工程で作りこんだ品質の不具合を後工程に流さないための管理表
と言えます。
品質管理の中心になる一番大切な書類であり、お客様に品質監査を受ける際は、QC工程表をベースに実施される非常に大切な資料です。(少なくとも私が監査に行く場合は毎回使っていました。)
製造が作成し、品質保証部が承認する所も多いと思います。大切な資料だけに設計/開発部門も作成には参加した方が良いと考えています。
QC工程表の基本構成
- 工程名
- 管理特性:品質に影響する製造の条件、管理すべき条件
- 品質特性:確認すべき品質、その工程で作りこむ品質、変化する品質は何か?
- 検査内容
- 判定基準:何を基準にして判定するか(限度見本、○○基準書、等)
- 管理基準:合格範囲が明確に分かるように表記する(○○±〇度 等)
- 管理項目/検査項目の管理方法:測定方法、頻度、担当者、責任者
- 記録:結果をどの記録に残すか?
- 異常時の処理:トレーサビリティをもとにグレーロットの隔離、全数検査などの処置
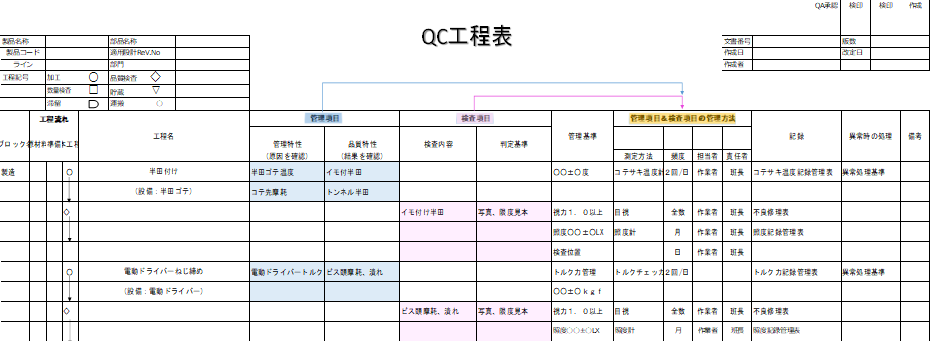
ネット:日本のものづくり~品質管理、生産管理、設備保全の開発、匠の知恵 から
QC工程表を作るには?

QC工程表を作るとは、設計開発により明確になったインプットを、具体的な品質特性や管理特性に落とし込み、測定頻度、判定基準、管理基準を決めて行く変換工程を経て、アウトプットとしてQC工程表にまとめる作業になります。
品質特性/検査内容/判定基準
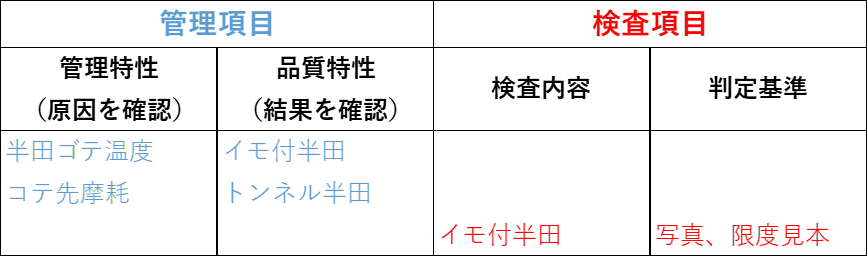
品質特性はその工程で作り込む品質ですので、結果になります。検査内容と判定基準を決める事になります。
品質特性は製品仕様に直接関係する特性か、関係しない特性かで判定基準を変える
- 関係する工程:工程内の判定基準は製品スペックよりも厳しめに設定する
- 関係しない工程:工程が作り出す機能を考え、現状維持の判定基準を設定する。
たとえば、ガラスの研磨を粗研磨、仕上げ研磨と2段階で実施する場合、
仕上げ研磨での板厚はお客様に届く製品の板厚そのものになりますので製品スペックよりも厳しく設定する必要が有ります。
しかし、粗研磨の場合、板厚は次の仕上げ研磨で調整可能なので現状維持を基準とすればよい事になります。
なお、工程監査をお客様から受けるような場合、通常はQC工程表に基づいて監査がなされます。お客様に提出するQC工程表は丸裸で出すと4M変更の縛りなども増え、非常に厄介なことになります。
現実的な対応として、社内用とお客様用と分ける事も大切になります。
管理特性/管理基準
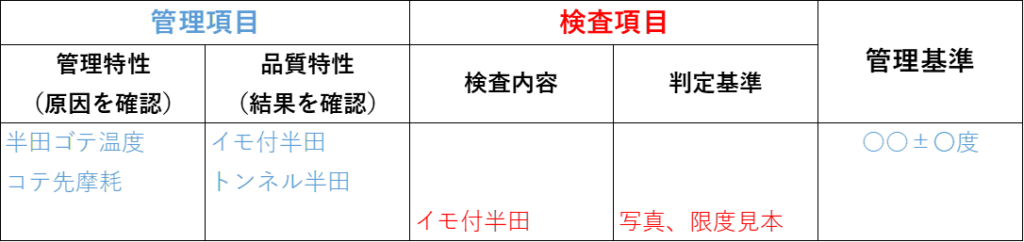
管理項目は品質特性を実現させる製造条件の事です。上記の例で言えば、半田ゴテ温度を○○±〇度、と決める事です。ガラスの研磨を行う場合は加工圧力や回転数、砥粒の濃度、等がそれです。
管理項目の管理基準は、設計/開発の設計検証で明確にしていくものです。しかし、実際に量産をしていくと実績も増え、管理基準を単純に広げても問題ない場合は良くあります。
常に見直す姿勢は大切になります。
品質特性の測定頻度
検査は基本全数検査です。しかしながら、全数検査を行うには当然、時間とお金がかかります。また、材料の強度評価のように一般に破壊検査と呼ばれる検査もあります。
測定頻度は工程能力とAQLを参考にし、品質の重要性、検査コストを考慮して総合的に決めて行く事になります。
工程能力Cpk
ネットで調べればすぐに出てくるので説明は省略しますが、どれだけ、安定してして生産出来ているかを示す指標で、1.33以上で工程能力は十分(10000個検査して不良は7個レベル)と言われています。
抜き取り検査を実施するには工程能力は1.33以上が必要とも言われていますが、見逃しが許される品質、許されない品質、品質的には規格のどちらかを狙った方が良いので目標値をどちらかに寄せている場合など、単純に工程能力だけで判断しないで指標と考えるべきだと思います。
下記の①、②を考慮し、総合的に判断、工程能力が低い場合は改善に注力
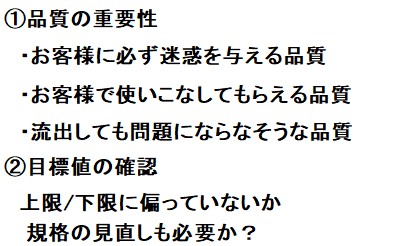
工程能力が高くなれば、抜き取り頻度も少なくて良いですが、工程能力が低ければ、当然抜き取り頻度も増やし、場合によっては全数検査が必要になります。
AQL(Acceptable quality level:合格品質限界、合格品質水準)
工程能力はあくまでもどれだけ安定して生産出来ているかを示す指標ですので、ロットの合否判定には使えません。
抜き取り検査である以上、有る確率で不良品が流出するのですが、その許容できるレベルを決めて、抜き取り数と合否判定基準を決める必要が有り、その際に用いられるのがAQLの考え方です。
以下の表では検査基準;なみ検査、不良混入率1.0%を想定した場合、K(1201個~3200個)がロット内のサンプル数だとするとその中から125個を測定し、NG品は3個まで合格、4個発生すればNGとするものです。ロット内のサンプル数は見やすくするために、アルファベットで代表されています。
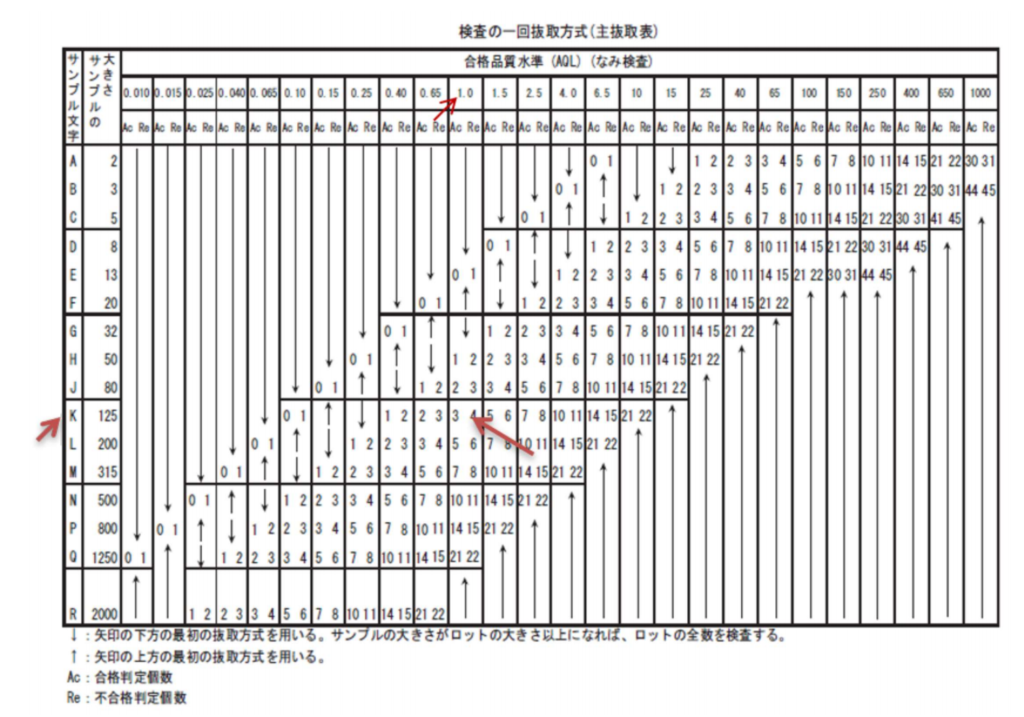
AQLの考え方をそのまま踏襲すると、ロットが大きくなりすぎる傾向が有り、忠実に守るのは難しい所が有ります。ロットサイズを小さくすると全数検査とほとんど変わらなくなります。
実情に合わせて運用による工夫をすることが大切になります。
そもそも、抜き取り検査では不良は取り除けない前提に成り立っていますので、実情に合った抜き取り数を決める事も大切です。
運用による工夫
述べてきたように、工程能力やAQLだけで抜き取り頻度を決めようとすると実際には非常に検査コストがかかったりします。
なので、運用に際して、ばらつきが大きくなったっり、平均値がずれるような事が考えたられる場合は測定頻度を増やす。などの工夫が必要になります。
休止明けのつくり始めは、諸条件が安定せず、不安定な事も追いのでN数を多くする。あるいは4Mの変化点で抜き取り枚数を増やすなどの工夫が必要となります。
- 最重要:品質の重要性、議論になりやすい
- 議論時の材料:工程能力、AQL、検査コスト、検査時間等
- 運用による工夫:作り始めの不安定なときには多めに、等、
FMEA評価結果
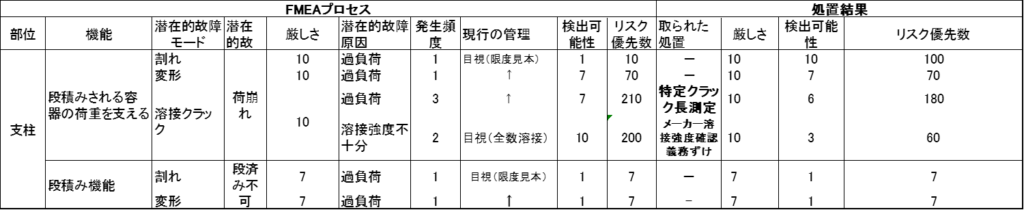
FMEA評価で得られた結果を反映させることが大切になります。
上記のように、私がやっていたような梱包容器の場合、取られた処置である、特定クラック長さ、溶接強度を抜き取りで確認するなどの処置を、品質特性、検査内容、判定基準、検査頻度をQC工程表に盛り込むという事です。
結局、QC工程表を作るうえで大切なことは?
- 製品仕様に関係する品質は、工程内検査は厳しめに設定する。
- 製品仕様に直接関係ない品質は、現状維持の基準を設定する。
- 検査は全数検査が基本、検査コスト/時間、品質の重要性、工程能力、等を考慮し総合的に抜き取り検査数を設定する。
- 品質を確実にする製造条件(管理項目)の管理基準は設計検証で明確にすべきであるが、量産後も常に見直す姿勢は大切になる。
- FMEAの評価結果を確実反映させる。
コメント