信頼性、信頼性設計とは
- 信頼性とは
- JIS Z8115ではアイテムが与えられた条件の下で,与えられた期間,要求機能を遂行できる能力と定義されています。
- 信頼性設計とは
- 必要な期間、故障せず使えるように設計する事と言えます。
- 従って、必要な期間(目標寿命)あるいは必要な使用回数を決めることも大切になります。
信頼性設計を進めるには図1のような手法を使って、設計にしっかり反映させることが大切と言われています。
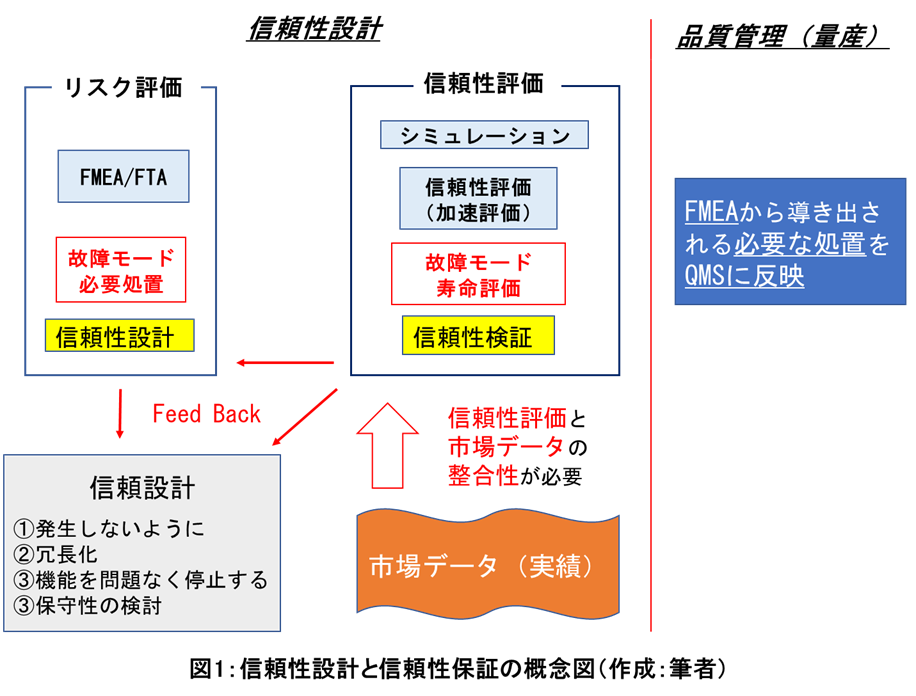
実際にその通りなのですが、厄介なのは、信頼性評価もシミュレーションも市場のデーター(実績)と比較しながらテスト条件やシミュレーション条件を調整しないと、精度が著しく落ちる(使えない)といった問題が発生します。
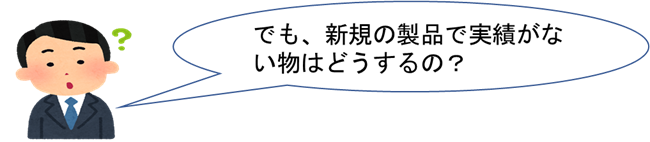
その問題に対して、個人的に進めていた方法を紹介します。
信頼性の市場データが活用できる場合
故障の分類
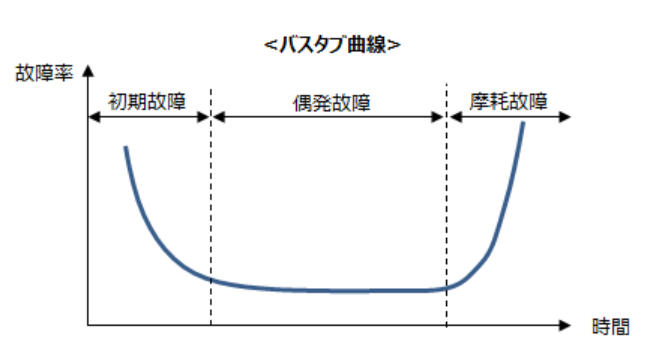
- 運転開始後、しばらくは故障が多い。これは設計、製造、据え付けなどで潜在していたものが顕在化するからである。
- 初期評価での故障は、お客様での使われ方、使用環境の調査不足が原因である事が経験上、ほとんどです。
初期に検出できなかったもの、あるいは偶発的要因によるものが主体で故障率は時間的にほぼ一定になる。
摩耗や、変形が起こり、パラメーター値の変化などによる劣化。いわゆる寿命によるものである。
参考図書:設計開発の品質マネジメント 久米 均著 日科技連
- 故障率は上記のように、時間(時期)によって、故障モードが異なり、バスタブ曲線を描くと言われています。
- 時期によって故障モードが異なるので、それに応じたリスク評価、信頼性評価を行う必要が出てきます。
リスク評価(FMEA/FTA)について
FMEAは文字通り、故障モードを想定して、それの対策を考えるといった手法ですので、信頼性設計そのものとも言えます。
しかし、FMEAは想定している範囲内の事しか評価出来ません。
従って、量産する前に、実際に加速評価やシミュレーションを行う事で、想定通りか、想定外の事が起こらないか検証する必要が出て来ます。
信頼性評価/シミュレーションについて
JISなどを見ると、何らかの信頼性評価方法が規定されています。しかしながら、その評価の前提となるテスト条件に当てはまらないケースが新しい開発品では良くあります。
そのような場合、JIS等の方法を参考にして、試験条件、シミュレーション条件を決める必要が有ります。
改めて言うまでもなく、試験条件を決めるには、製品が使われる環境を良く調べ、市場で起きた不具合が信頼性試験で再現できるか確認する事が大切になります。
信頼性設計
実際に、信頼性設計については以下のような優先順位で進めるのが良いと言われています。リスク評価、信頼性評価結果を踏まえて、必要があれば設計を見直しましょう。
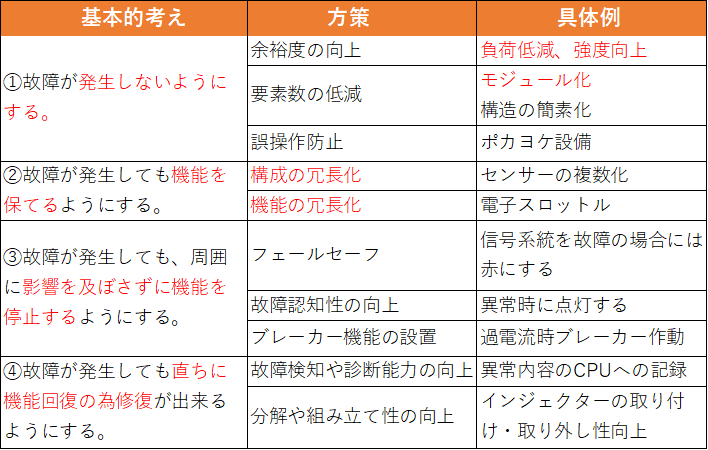
過去の市場のデータや経験が活用できない場合
部品、モジュールとしての信頼性評価
実績のある部品(市場データのある部品)の活用、構造の簡略化、新規部品の場合には、サプライヤーに評価を依頼する事が大切と言われています。
参考図書、設計開発の品質マネージメント、久米 均 日科技連 、トヨタ必須の17の品質管理手法を伝授 品質の教科書 皆川 一二 日経BP
部品、モジュールとしての信頼性評価 が効果的でない場合
初期故障対策
故障モードは初期故障、偶発故障、摩耗故障の三つのモードがあると説明いたしました。故障の発生しやすい初期故障と、摩耗故障を優先的に考える必要が有りますが、初期故障は経験からお客様での使われ方、輸送中も含めた使用環境の調査不足が原因である事が、経験上ほとんどです。
使用環境やお客様の使われ方を想定した強調試験により、初期に発生する故障モードを確認する事は可能であるが、いずれにしても、お客様の使われ方や使用環境の精度により結果の精度は異なります。
従って、信頼性評価よりもお客様としっかり事前協議することが非常に大切になります。以下の記事に詳しく記載していますので参考にしてください。
摩耗故障対策
私が実施していたガラスの梱包容器の信頼性設計、品質保証の概念図を図2に示します。摩耗故障故障が発生するのには時間がかかるので、その間に改めて信頼性を評価するのです。
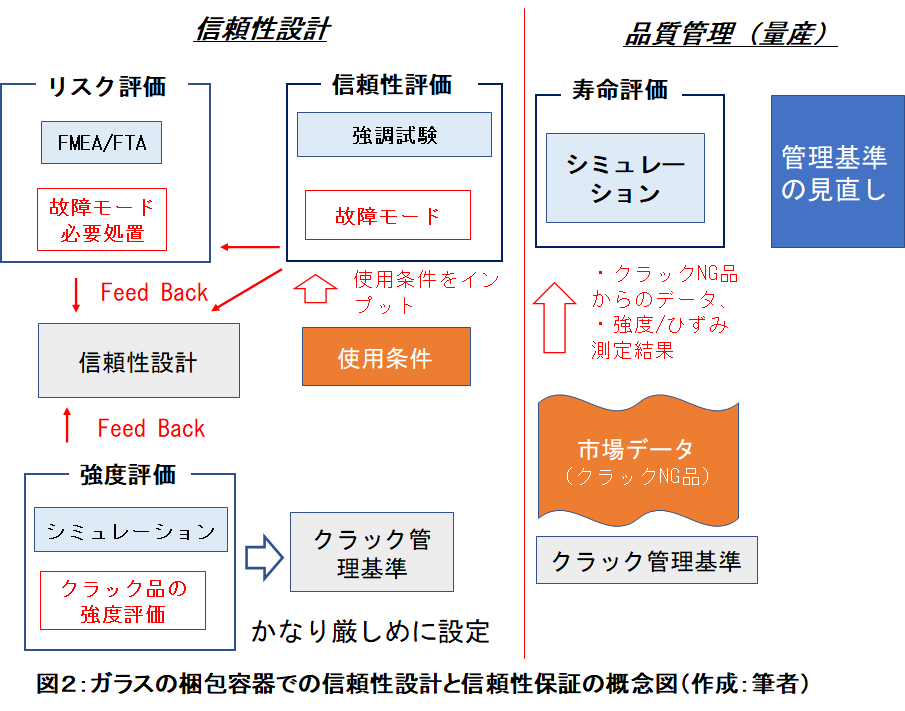
私が扱ったガラスの梱包容器の場合、お客様と工場を往復するため、工場で管理できるといったメリットが有ります。
設計の段階での信頼性評価は初期故障向けと割り切り、摩耗故障については、強度のシムレーション結果からクラックの管理基準をかなり厳しめに設定し、量産時にNG品を分析、強度評価を行い、その結果をシミュレーションに反映させ、寿命をシミュレーションし、管理基準の見行いました。
お客様の工程に据え置きになるような装置であれば、出荷前に寿命評価は必須になると思います。ただ、装置などであれば、部品、モジュールとしての信頼性評価が有効になるとも思います。
また、寿命評価と言えば、加速評価により、故障の発生率を調べるのが一般的かと思いますが、ワイブル解析するにはそれなりのN数が必要になり、お金と時間が非常にかかります。私は、それだけの価値が得られないと考え実施はしませんでした。
状況に応じて、必要な評価方法を考えるのは大切だと思います。
まとめ
- 信頼性設計
- FMEAは故障モードを想定しているので信頼性設計をしているともいえる
- 信頼性検証
- FMEAは人が想定している範囲内に限られるので、設計検証として、信頼性評価が必要になる
- 信頼性評価はいずれにしても加速評価になるので、市場のデータ(実績)と整合性が取れている事が必要になる。
- 故障には、量産開始直後に発生が多い、初期故障、安定期の偶発故障、摩耗や変形によるいわゆる摩耗故障(寿命故障)と時期のよってモードが異なる。各モードに応じた対策が必要である
- 初期故障は、お客様での使われ方、使用環境の調査が不十分であることが主原因
- 初期故障
- お客様の使われ方や使用環境の調査不足が主原因であり、その対策を優先する。
- 寿命評価(摩耗故障対策)
- 部品、モジュールで実績のある部品を使う。新規の部材は、その部材の評価をサプライヤーから入手する
- 量産で市場の結果が出てきたところで改めて寿命評価を改めて行う。
コメント